When choosing a desiccant dryer process, it is of vital importance to identify the drying performance of the material. Materials can be divided into two types: hygroscopic and non-hygroscopic. Hygroscopic materials can absorb moisture from the surrounding environment, while non-hygroscopic materials cannot absorb moisture from the environment. For non-hygroscopic materials, the moisture existing in any environment remains on the surface, becoming "surface moisture" and easy to be removed. However, rubber particles made of non-hygroscopic materials may also become hygroscopic due to additives or fillers. Convection dryer can use a hot air dryer to dry non-hygroscopic materials. Because the water is only loosely constrained by the interfacial tension between the material and the water, it is easy to remove. The principle of this type of machine is to use a fan to absorb the air in the environment and heat it to the temperature required to dry a specific material. The heated air passes through a drying hopper and heats the material by convection to remove moisture. It is generally best to use microwave drying equipment for drying hygroscopic materials: the first drying section focuses on the inside of the material; the second drying section evaporates the moisture on the surface of the material. At this time, the drying speed slows down and is dried. The temperature of the material begins to rise; in the last stage, the material reaches a moisture absorption balance with the dry gas. At this stage, the temperature difference between inside and outside will be eliminated. 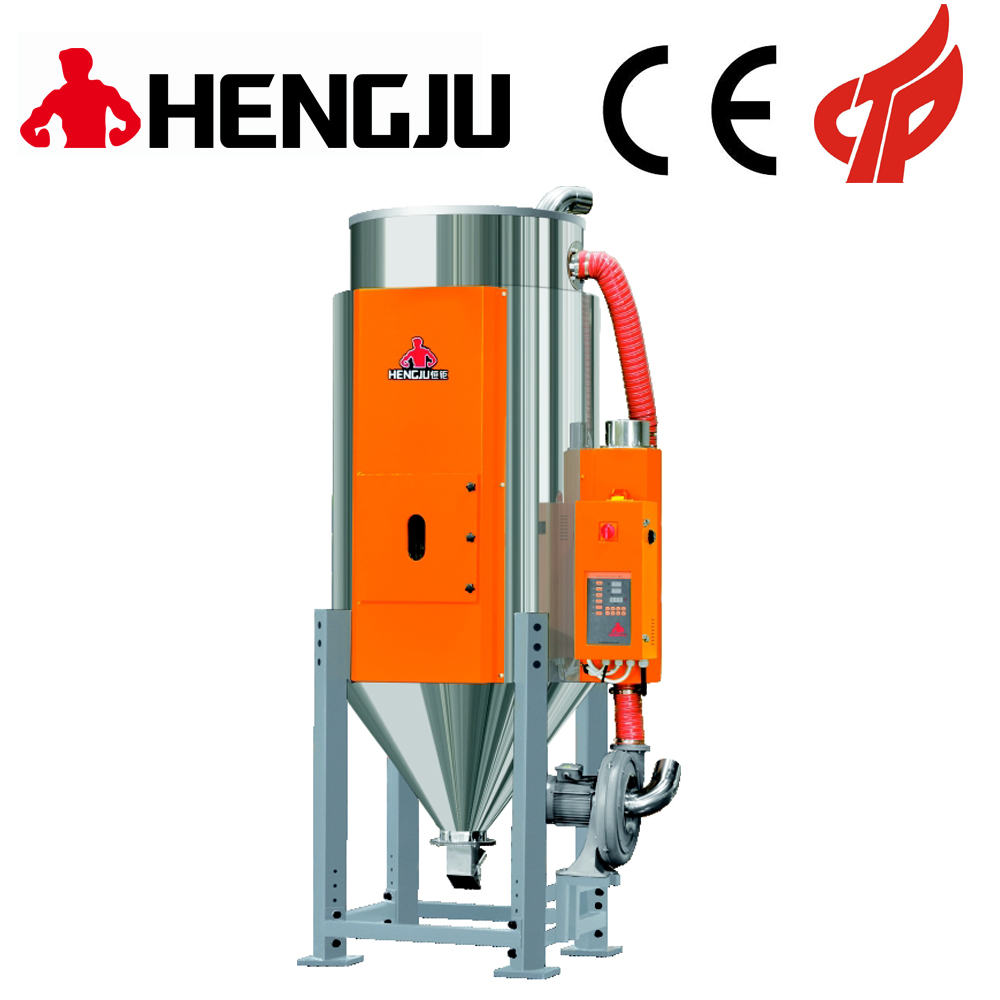 At present, the most common way to produce dry air is to use a dry gas generator. The equipment is based on an adsorptive dryer composed of two molecular sieves, where the moisture in the air is absorbed. In the dry state, the air flows through the molecular sieve, and the molecular sieve absorbs the moisture in the gas to provide dehumidifying gas for drying. In the regeneration state, the molecular sieve is heated by hot air to the regeneration temperature. The gas flowing through the molecular sieve collects the removed water and brings it to the surrounding environment. Another way to generate dry gas is to reduce the pressure of compressed gas. The advantage of this method is that the compressed gas in the supply network has a lower pressure dew point. After the pressure drops, its dew point reaches about 0°C. If a lower dew point is required, a membrane or adsorption dryer can be used to further reduce the dew point of the air before the compressed air pressure is reduced. In dehumidified air drying, the energy required to produce dry gas must be calculated additionally. In adsorption drying, the molecular sieve in the regenerated state must be heated from the temperature of the dry state (about 60°C) to the regeneration temperature (about 200°C). To this end, the usual practice is to continuously heat the heated gas to the regeneration temperature through the molecular sieve until it reaches a certain temperature when it leaves the molecular sieve. Theoretically, the energy necessary for regeneration is composed of the energy required to heat the molecular sieve and the water adsorbed inside, the energy required to overcome the adhesion of the molecular sieve to water, the energy necessary to evaporate water and the temperature of water vapor to heat up.
|