PET dehumidifying dryer |
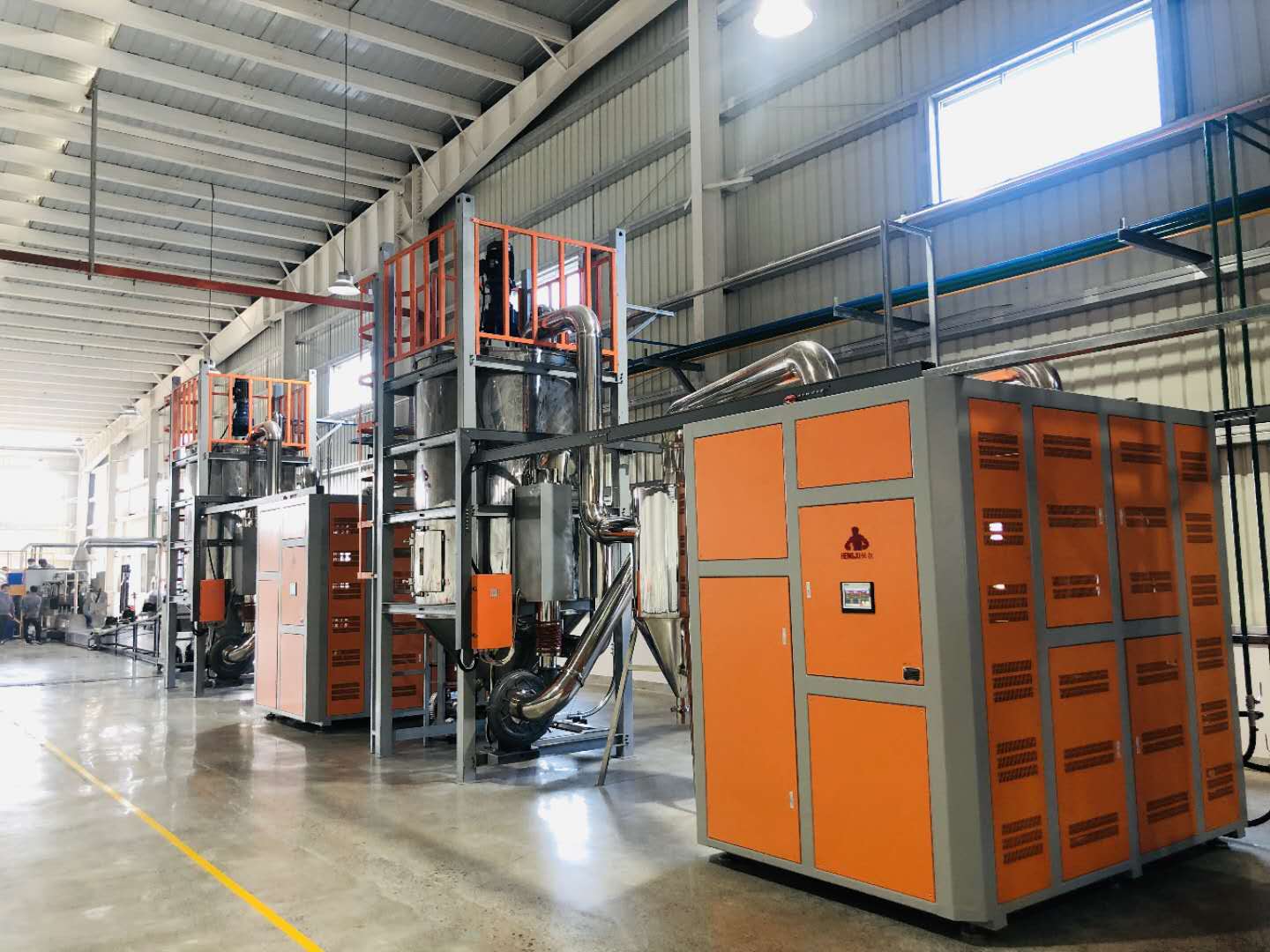 |
product name:PET dehumidifying dryer |
release time:2020-12-23 13:57:45 |
Numbering:PET dehumidifying dryer-001 |
Brand:HENGJU |
Price:¥By function |
weight :By function |
unit weight:Kg/set |
manufacturer:hengju |
patent:hengju |
Producing country: |
simple description:This is an automated mechanical equipment used to dehumidify and dry PET particles and PET powder materials. It can also be used to dehumidify and dry various plastic or resin particles and powder materials. For example: PET, PA, PE, PC, PMMA, PLA, PA66, HDPE... |
Product alias:PET dehumidifying dryer,dehumidifying dryer,plastic dehumidifying dryer,PET desiccant dryer |
|
|
What is PET PET material, the full name polyethylene terephthalate, is usually called polyester resin, which is the most important variety in thermoplastic polyester. Abbreviated as PET or PEIT Polyester is a milky white or yellowish highly crystalline polymer with a smooth and shiny surface. Creep resistance, fatigue resistance, good friction resistance and dimensional stability, low abrasion and high hardness, with the largest viscosity in thermoplastics; good electrical insulation performance, less affected by temperature, increased by nucleating agent, crystallizing agent and glass fiber Strong improvement. In addition to the properties of PBT, PET also has the following characteristics: 1. Heat distortion temperature and long-term use temperature are the highest among thermoplastic general engineering plastics; 2. Because of its high heat resistance, when the reinforced PET is inserted into the solder bath at 250°C for 10 seconds, it hardly deforms or discolors. It is especially suitable for preparing soldered electronic and electrical parts; 3. The bending strength is 200MPa, the elastic modulus reaches 4000MPa, the creep and fatigue resistance are also very good, the surface hardness is high, and the mechanical properties are similar to those of thermosetting plastics;. PET is mainly used for fibers, and a small amount is used for films and engineering plastics. PET fiber is mainly used in the textile industry. PET film is mainly used for electrical insulation materials, such as capacitors, cable insulation, printed circuit wiring substrates and electrode tank insulation. Another application field of PET film is film base tape and base tape, such as motion picture film, X-ray film, audio tape, computer tape and so on. PET film also uses vacuum aluminum to make metallized films, such as gold and silver wires, and miniature capacitor films. Another use of PET is blow molding products, polyester stretch bottles for packaging. Glass fiber reinforced PET is suitable for electrical, electronic and automotive industries. It is used in various coil formers, transformers, TVs, tape recorder parts and casings, car lamp holders, lamp shades, incandescent lamp holders, relays and rectifiers. It is odorless and aroma-preserving, safe in food hygiene, beautiful and easy to shape, and has been widely used in food containers. |
Dehumidification and drying temperature of PET material PET is a crystalline resin with a specific gravity of about 1.4kg/L, a melting point of 245°C, and a molding temperature of about 290-315°C. The particle bulk density is 0.8~0.85kg/L, and the sheet bulk density is 0.38~0.4kg/L. The main uses of PET are in the fields of synthetic fibers, PET bottles and film sheets. In recent years, with the economic development, people’s awareness of environmental protection has increased. As a packaging material, PET sheets are replacing PVC packaging materials that are difficult to recycle. The aspect shows good development potential. Drying temperature Because PET is highly hygroscopic, drying before processing is necessary. The recommended drying condition is 120~165℃, 4~6 hours drying treatment. If it is a sheet extrusion line, the moisture content after drying should be less than 200ppm; if it is a preform production line, it should be less than 50 ppm after drying; conventional spinning is less than 50ppm, and high-speed spinning is less than 35ppm. temperature Generally, the higher the drying temperature, the higher the drying rate; the shorter the drying time, the lower the moisture content of the raw material after drying. The drying temperature of the stirred crystallizer is usually between 120~160℃. Dehumidification drying temperature is between 160~180℃. time The crystallization time is 1 to 2 hours, and the crystallization time is inversely proportional to the pre-crystallization temperature. The drying time is 4~6 hours to make the water content of PET approach or reach the equilibrium water content; the drying time is related to the drying temperature, vacuum degree, and moisture content of dry air. 1. Injection grade ①Temperature setting: Nozzle: 280~295℃, front section 270~275℃, middle forging section 265~275℃, rear section 250-270℃; screw speed 50~100rpm, mold temperature 30~85℃, amorphous type The mould is below 70℃ and the back pressure is 5-15KG. ②Try the desiccant dryer, the material tube temperature is 240~280℃, the injection pressure is 500~1400℃, the injection molding temperature is 260~280℃, the drying temperature is 120~140℃, and it takes 2~5 hours. 2. Film grade Firstly, the PET resin chips are pre-dried to be hydrolyzed, and then the amorphous thick flakes are extruded through a T-die in an extruder at 280°C, and then quenched by a cooling drum or cooling liquid to keep them in an amorphous state. In order to stretch orientation. The thick film is then biaxially stretched by the tenter to form a PET film. Longitudinal stretching is to preheat the thick sheet to 86~87℃, and stretch it about 3 times along the plane extension direction of the thick sheet at this temperature, so that its orientation can increase the crystallinity and reach a higher temperature: transverse stretching preheating temperature 98~100℃, stretching temperature 100~120℃, stretching ratio 2.5~4.0, heat setting temperature 230~240℃. The film after stretching in the vertical and horizontal directions needs to be heat-set to eliminate the film deformation caused by stretching and make a film with better thermal stability. 1. Polyparaformaldehyde glyceride (PET) slices are dried in a vacuum oven at 80°C for 3 hours and 130°C for 8 hours 2. Isothermal drying, initial 6h at 110℃ in vacuum oven 3. Dry 6.5h at 90℃, 0.001MP 4. Keep it at 90℃ for 2h to pre-crystallize, then dry at 120℃ for more than 24h |
Working principle of PET dehumidifying dryer
The PET pre-crystallization dryer mainly relies on the vibration exciter from the bottom of the container to generate mechanical excitation force, so that the container generates periodic vibration force. Because the inner bottom of the PET pre-crystallization dryer container is a cylindrical shape, the amplitude of each point is different, so that the material in the PET pre-crystallization dryer container revolves around the center axis of the container, and then rolls around the center of the PET pre-crystallization dryer cylinder, forming a ring Spiral movement to achieve a dry state. The dried material is in contact with the inner wall of the jacket-heated container to transfer heat and increase temperature. After reaching the vaporization point, the moisture is vaporized and discharged under vacuum, so that the material can be quickly dehydrated and dried. The internal circulation process of PET dehumidification and drying: through the operation of the compressor → discharge high-temperature and high-pressure gas through the exhaust port → enter the condenser for cooling → become low-temperature and high-pressure gas → pass series interception → become low-temperature and low-pressure liquid → evaporate and suck through the evaporator Heat → return to the compressor to become a low-temperature and low-pressure gas. This cycle alternates. The entire process of PET dehumidification and drying is automatically completed by the dehumidification dryer, so the characteristics of the PET dehumidification dryer are as follows: First, the raw material contact surface is all stainless steel design; Second, the precision die-cast aluminum shell has a smooth surface and good heat preservation performance; Third, a silent fan, optionally equipped with an air filter, to ensure the cleanliness of the raw materials; Fourth, the barrel body and machine base are equipped with viewing windows to directly observe the internal raw materials; Fifth, the curved design of the electric heating cylinder avoids burning caused by the accumulation of raw material dust; Sixth, the proportional deviation indicating temperature controller is used to accurately control the temperature; PET dehumidification and drying is an essential step in the plastics processing industry. If the working time and working cost are effectively shortened in this step, it will be able to reduce the overall cost of plastic processing. Advantages of PET pre-crystallization dryer: 1. Large material handling capacity, low fuel consumption and low drying cost. 2. It has the characteristics of high temperature resistance and can use high temperature hot air to quickly dry the material. 3. Strong anti-overload ability, stable running of the cylinder and high reliability. 4. With the self-aligning tug structure, the tug and the rolling ring cooperate well, which greatly reduces wear and power consumption. 5. Strong expandability, the design takes into account the production margin, even if the output increases slightly, there is no need to replace the equipment. |
PET dehumidification dryer application With the widespread use of engineering plastics, dehumidifying dryers have gradually replaced traditional hot air dryers. PET desiccant dryer can also be used, For example, POM, ABS, TPE, PAL, ABS, CAB, EVA(2), EVOH, LM(4), LCP, PA11, PA6.46.6, PAI, PAR, PBT,Pla,HDPE,PA PC,PC/ABS,PC/PBT,PE.HDEPE,LDPE black3%,PE.HDEPE.LDPE black40%,PEEK,PE(1), PEN,PES,PET,PETG,PI,PMMA,POM,PP,PPO,PPS,PS,[GPPS.EPS.HIPS],PSU,PIT,PUR, PVC,SAN,SB,TPE,TPE,TPO,TPU,
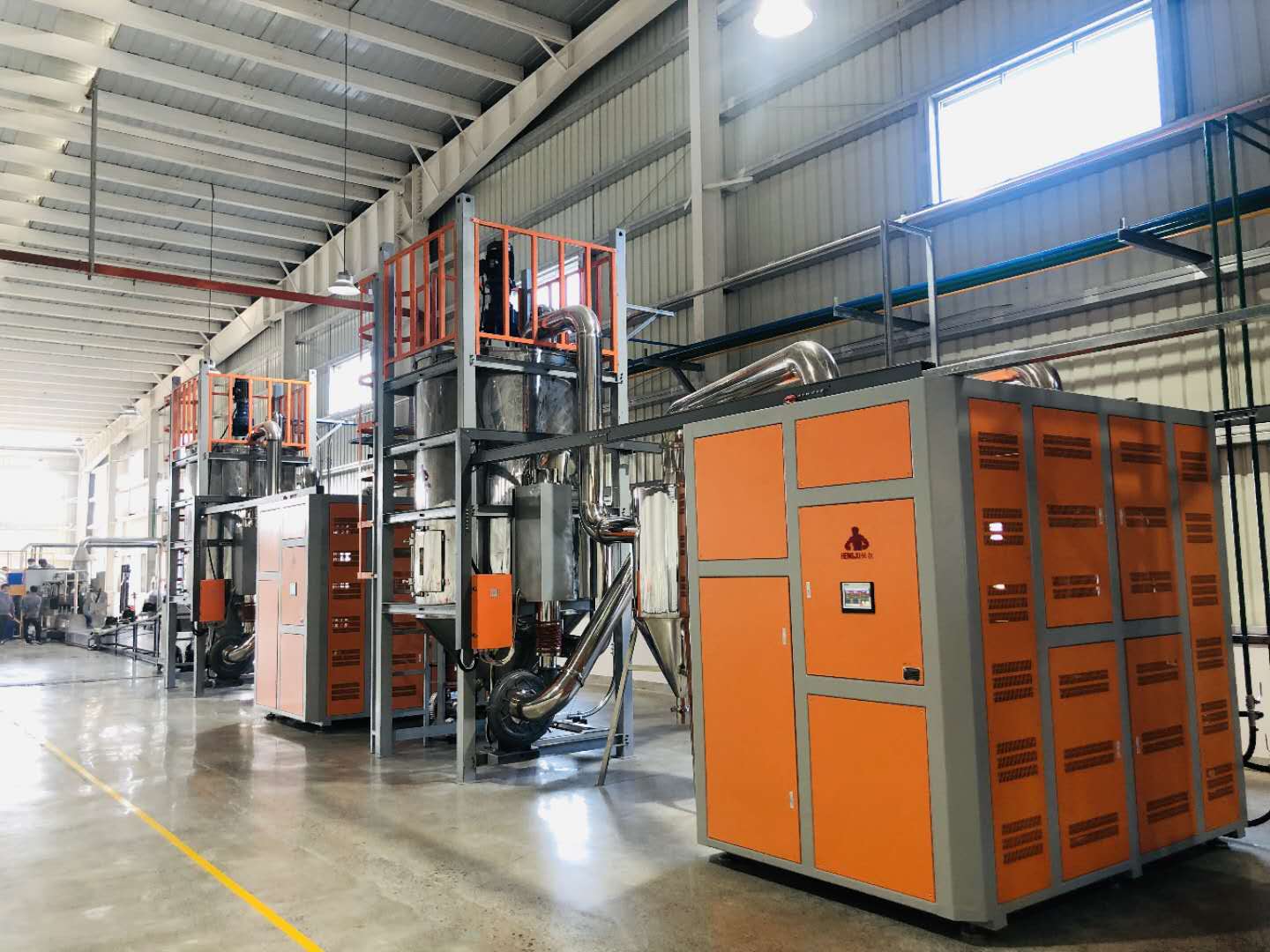 Other plastic or resin materials; Table for Drying Time and Temperature by Material
Material |
Initial Moisture Content |
Drying Time |
Drying temp. |
ABS Acrylonitrile Butadiene styrene |
0.6% |
2~3 H |
80℃ |
PA 6 Polyamide 6 |
1% |
4~6 H |
75℃ |
PA 66 Polyamide 66 |
1% |
4~6 H |
75℃ |
PA 6, 10 Polyamide 6, 106 |
1% |
3~4 H |
75℃ |
PA 11 Polyamide 11 |
1% |
3~4 H |
75℃ |
PA 12 Polyamide 12 |
1.8% |
2~3 H |
75℃ |
PC Polycarbonate |
0.36% |
2~3 H |
120℃ |
PE Polyethylene |
0% |
1 H |
90℃ |
PE Polyethylene w/carbon black |
0.5% |
3~6 H |
85℃ |
PET Polyethylene Terephthalate |
0.4% |
3~6 H |
160℃ |
PETG Polyethylene Terephthalate Glycol |
0.1% |
6 H |
66℃ |
PBT Polybuthyleneterephthalate |
0.4% |
3 H |
160℃ |
PI Polyimide |
0.32% |
3 H |
120℃ |
PMMA Polymethylmethacrylate |
0.7% |
2~4 H |
80℃ |
PSU Polysulfone |
0.22% |
3 H |
120℃ |
POM Polyoxymethylene |
0.25% |
3 H |
100℃ |
PP Polypropylene |
0% |
1 H |
90℃ |
PPO Polyphenyleneoxide (Norl R) |
0.13% |
3 H |
120℃ |
PS Polystyrene |
0% |
1 H |
80℃ |
PUR Polyurethane |
0.9% |
3 H |
90℃ |
PVC Polyvinyl Chloride |
0.4% |
1 H |
70℃ |
SAN Styrene Acrylonitrile Copolymer |
0.3% |
2~3 H |
80℃ |
SB Styrene Hi-impact |
0.6% |
2 H |
80℃ |
lonomer(SurlynR) |
1% |
2~8 H |
50℃ |
VPE Crosslinked Polyethylene |
2% |
6 H |
50℃ |
KODAR PETG 6763 |
1.8% |
4 H |
66℃ |
PES Polyester |
0.6% |
4 H |
75℃ |
CA Cellulose Acetate |
1.3% |
2~3 H |
75℃ |
CAB Cellulose Acetate Butyrate |
1.3% |
2~3 H |
75℃ |
CP Cellulose Propionate |
1.3% |
2~3 H |
75℃ |
lonomer |
1.4% |
2~3 H |
90℃ |
note: Since the melting point and characteristics of each material are different, the setting of the dehumidification and drying temperature and time on the machine and equipment is also different PET pellet dryer series are mainly designed for high-efficiency dehumidification of engineering plastics with strong hygroscopicity. Using the honeycomb runner with ceramic fiber as the base material, which represents the highest technological achievements of today, as the core component, the dry air provided can easily reach -40℃ dew point, and ideally it can reach -50℃ or even lower dew point , And the dew point temperature is stable, ensuring the high quality and stability of the molded plastic products. The whole series adopts P.LD. temperature control system as standard equipment; also provides PLC control with LCD touch-sensitive human-machine interface and can monitor the dehumidification effect of the machine Dew point meter is optional, the maximum drying air volume of this product can reach 3000m3/hr. The plastic before molding must be dried to an orientation ratio of less than 0.02%, which is completely bad, sprue adhesion, burrs, bubbles, silver bars, flow marks, cracks, dimensional stability and internal stress. Product defects (for example, insufficient physical properties and strength) are caused by sufficient dehumidification of the plastic before molding. Especially for PET, PBT, PA, PC and other high water absorption plastics, drying equipment with an ultra-low dew point of -40°C is required. Plastic Granule dryer, can be dried to a volume ratio of less than 0.02%, which solves the shortcomings of short circuit, gate adhesion, bubbles, silver bars, cracks, poor dimensional stability, internal stress and insufficient physical strength of the product. There are a lot more. Mainly used in plastic products, automobiles, optical discs, experiments, communications, optics, etc.; the rotary honeycomb can reach a low dew point of zero for dehumidification and drying at -40°C. In the case of enhanced configuration, the dehumidification dew point can be as high as -50°C. It is a choice for high-precision industries. |
PET dehumidifying dryer operating instructions ①. Temperature measurement and control range: 0-180 degrees ②. Heating, PID temperature control method ③. 24-hour real time display ④. Nine sections of timing on and off function ⑤. Power-on delay and power-off delay ⑥. Automatic power-on time setting: In the case of power-on, press the "SET" button to set the light on, and then press the "Timer" button again, then "ON1" will be displayed on the PV, and then press the "Timer" button again. “ON2” is displayed on the PV, and so on, it is displayed cyclically between “ON1~ON9”, and at this time, the corresponding automatic power-on time is displayed on “TIME” in a flashing manner. At this time, you can press the “plus” or “minus” button. "Key" and "Shift key" can modify the current set value. After finishing the setting, press the "Set" button to exit and save the parameters. ⑦. Automatic shutdown time setting: Under the power-on condition, press the "SET" button to set the light on, and then press the "Delay" button again, then "OF1" will be displayed on the PV, and then press the "Delay" button. Then “OF2” will be displayed on the PV, and so on, it will be displayed cyclically between “OF1~OF9”, and the corresponding automatic shutdown time will be displayed on “TIME” in a flashing manner. At this time, you can press the “plus key” or "Minus key" and "Shift key" can modify the current set value. After finishing the setting, press the "Set" button to exit and save the parameters. ⑧. The time setting range of the automatic switch machine: 00 hours 00 minutes; the system can be started and shut down up to 9 times within 24 hours a day, and the next heating time must be later than the last heating shutdown time; the next heating shutdown The time must be within the same 24-hour period the last time the heating was turned on. ⑨. When the power is not turned on, pressing the "fan" and "heating" keys has no effect. When the fan is not turned on, pressing the "heating" button is invalid. After turning on the power, the "Fan" key is valid. After turning on the fan, turning on and off the "heating" key is effective. ⑩ . Over-temperature temperature: When the measured temperature on the PV is greater than this temperature setting, the system will stop heating and output an alarm at the same time. ⑪. There must be a wind chime as a reminder when operating the keys Drying part opening and closing process ①. When the power is on, the 3S countdown will be displayed on the PV, and the software version number will be displayed on the SV. After 3S, the word "OFF" will be displayed on the PV (this is the shutdown state) ②. Power-on process: In the shutdown state, at this time, press the on/off button, the PV and SV will immediately display the corresponding parameters, the power indicator light is on, and press the "fan" button at this time, the fan light is on, and the fan relay is activated , Press the "heating" button at this time, the heating lamp will be on, the heating relay will be PID output, and the heating output lamp will be on and off with the output of the heating relay (this is the startup process) ③. Shutdown process: 1. When shutting down directly by pressing the on/key: first turn off the heating, after the delay is over, turn off the fan after the delay, and then turn off the fan. During the delay, the PV will alternately display "OFF" and the current temperature. Finally back to the shutdown state. 2. When turning off the heating and the fan by pressing the fan button: first turn off the heating, and after the delay, turn off the fan after the delay, then turn off the fan, but will not turn off the display ④. Automatic startup process: first start the fan, while delaying 10S (starting heating delay time), and then start heating, the system controls the temperature in PID mode. ⑤. Automatic shutdown process: first turn off the heating, after the delay, turn off the fan after the delay, and finally display "OFF" and the current temperature alternately on the PV (during the automatic shutdown time period), and the power light and automatic operation The light is always on. The process of turning on and off the mixing part 1. Press the green button of the stirring switch on the electric control box when the stirring is on, and the mixer will start at this time. When starting, pay attention to the running direction of the mixer and whether it is forward rotation. The mixing machine keeps running after it is started. When it needs to be stopped, press the red button of the mixing switch on the electric control box to stop. 2. The mixer part and the dryer part are controlled independently. |
Precautions for PET dehumidifying dryer PET desiccant dryers usually use dry air to dry plastics to avoid moisture and moldy industrial plastics with strong hygroscopicity, which will affect the production and quality of plastic products. In order to expand the performance and performance of the dehumidification dryer, what is the maintenance method of the PET dehumidification dryer? 1. Please pay attention to the place where it is placed and used, and do not use it in an overly enclosed and narrow space. If there are objects around or above, please keep a distance of more than 50 cm. Do not use it in a place with a lot of oily smoke, otherwise it may cause the loss of electrostatic function. 2. The indoor temperature that the dehumidifier is suitable for is about 12℃~35℃. The function of the dehumidifier is the best time it can perform. If the indoor temperature is lower than 12°C, usually the humidity in the air is already very low. In order to avoid excessive drying and causing physical discomfort, it is recommended that you do not use a dehumidifier. 3. To clean the body of the PET dehumidifier, when dealing with the cleaning problem of the industrial dehumidifier, you must use a neutral detergent, or directly wipe the dehumidifier with a soft damp cloth. The body will cause varying degrees of injury. 4. After closing, please do not restart the PET desiccant dryer immediately. After stopping operation, you must wait three minutes before restarting to extend the replacement time of the compressor. Currently, the new dehumidifier has a self-protection function, so if you press the start button immediately after turning it off, it may not be usable. This is normal. 5. Ensure that the hot air is clean. 6. Measures should be taken to prevent coke dust and avoid backflow of hot air. 7. During the drying process of the material, all parts of the equipment in contact with the material must be cleaned and disinfected. 8. For viscous materials, measures should be taken to minimize sticking. 9. In order to improve the solubility, instant solubility, and dry products, they should be continuously discharged from the drying chamber quickly and packaged after cooling. 10. The exhaust air temperature is allowed to exceed the requirements to ensure product quality and safety. |
|