PET pre-crystallization dryer is the main crystallization equipment for plastic production and processing. Amorphous PET is prone to bonding when exposed to high temperature. The main purpose of crystallization is to prevent PET from drying and bonding at high temperature. Commonly used methods are to increase stirring while drying or use airflow to boil PET. The temperature continues to rise, and when it reaches 160°C, multiple molecular chains with intermolecular interactions undergo partial rearrangement, resulting in spherical crystals, that is, crystals.
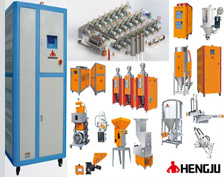 The maximum degree of crystallization of PET is about 55%, which can produce ordered crystalline regions. The crystallization temperature of PET desiccant dryer ranges from 120 to 220°C, the crystallization time is 1 to 2 hours, and the crystallization time is inversely proportional to the pre-crystallization temperature. The higher the drying temperature, the higher the drying rate; the shorter the drying time, the lower the moisture content of the raw material after drying. The drying temperature of agitated crystallizer is usually between 120~160℃. Dehumidification drying temperature is between 160~180℃. Use airflow to boil PET while drying. The higher the drying wind speed, the higher the relative velocity of PET and airflow, so the drying time will be shortened, but the dust generated by the system will increase accordingly, and it is necessary to consider removing too much dust.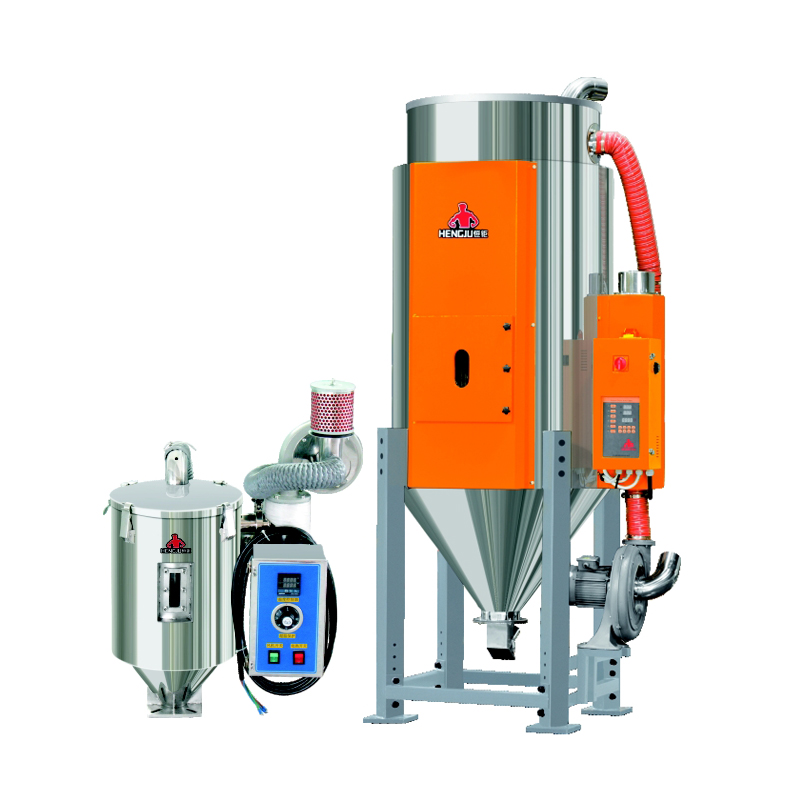 The lower the moisture content (dew point) of the hot air, the faster the drying rate of the raw materials, and the lower the corresponding equilibrium moisture of the raw materials. In the actual processing process, considering the processing cost and energy consumption, for the preform or injection molding, the dew point value is less than -50 ℃ to meet the dry moisture content of the raw material to be less than 50 ppm. For extrusion molding, the dew point value is less than -40°C to meet the requirement that the moisture content of the raw material is as small as 100 ppm.
|