The invention relates to the technical field of plastic drying equipment, in particular to a plastic particle dryer. Background technique: The plastics industry is an important part of the national economy. Plastics are polymer compounds that are polymerized through addition polymerization or polycondensation with monomers as raw materials, commonly known as plastics or resins. The composition and shape can be changed freely. It is composed of synthetic resins and It is composed of fillers, plasticizers, stabilizers, lubricants, pigments and other additives. The main component of plastics is resin. Plastics are used more and more widely, with light weight, high strength, corrosion resistance and easy processing. However, plastic particles Due to storage, it will absorb moisture in the air and make it damp. The chemical properties of plastic products made of damp plastic raw materials will be significantly reduced, which will affect the quality of the products. Due to the drying degree of the plastic particles and the transparency of the final product, Color purity, including bending, torsion, elasticity, tension index, and yield is related, so it is a very important link to dry the plastic particles before they are sent to injection molding machines, extruders, blister machines or other plastic processing machinery. In the existing drying process, the particles are unevenly heated, the temperature control is inaccurate, and the discharge port is easily blocked, which reduces the quality and work efficiency of the finished product. Technical realization elements: The main technical problem solved by the present invention is to provide a plastic particle dryer, which can fully dry the plastic particles to be processed and dry uniformly. The described plastic particle dryer includes a dryer base, the dryer base adopts a rectangular parallelepiped structure, the material is made of cast iron material, and the lower end of the dryer base is provided with friction stripes, which make the dryer more stable as a whole.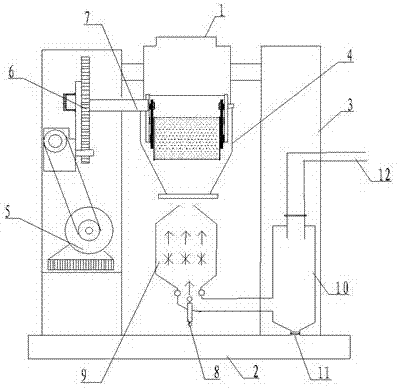 A dryer frame is set on the base of the dryer. The dryer frame is divided into a left bracket and a right bracket. The left bracket and the right bracket are hollow structures. A beam structure is connected between the left and right brackets. A hopper is set in the middle of the beam, a feed port is set at the upper end of the hopper, and a roller is set at the lower end of the hopper. During operation, the plastic particle materials are connected to the hopper. A swing motor is installed in the left bracket. The swing motor is connected to a reducer through a pulley. The reducer is installed in a gear box. A universal drive shaft is installed on the gear box. The universal drive shaft is connected to the drum swing shaft through a swing rod. The other end of the roller swing shaft is connected with the roller as a whole. A sieve hole is set on the outer wall of the drum, and the sieve hole is stirred to make the particles fall from the hopper, so that the particle material falls uniformly. A discharge port is set at the lower end of the hopper, and the discharge port corresponds to the direction of the plastic bin A. A preferred technical solution is that the discharge port of the hopper is equipped with an electronic control valve, which is convenient to control the speed of particle feeding. The particles of the hopper directly fall into the plastic warehouse A. The plastic warehouse A adopts a hexahedral structure. The top of the plastic warehouse A is set to open mode, and the bottom of the plastic warehouse A is equipped with a blower pipe. The blower pipe is connected with a hot blower motor. The warehouse A is connected to the plastic warehouse B through the conveying pipe. The plastic particles enter the plastic warehouse B through the conveying pipe. A hot air outlet is set at the top of the plastic warehouse B. The air is discharged from the hot air outlet. A particle outlet is set at the lower end of the plastic warehouse B. The particles are discharged from the particle outlet. In a preferred technical solution, a collecting bucket is arranged at the particle outlet to facilitate the collection of plastic particles. The beneficial effects of the present invention are: a plastic particle dryer of the present invention has a compact structure design, sufficient drying effect, can avoid corrosion to subsequent equipment, and stable and reliable operation of plastic particles. Description of the drawings Figure 1 is a schematic diagram of the structure of a plastic particle dryer of the present invention; The parts in the drawings are marked as follows: 1 is the feed inlet, 2 is the dryer base, 3 is the dryer frame, 4 is the drum, 5 is the swing motor, 6 is the swing rod, 7 is the drum swing shaft, 8 is the blower pipe, 9 is the plastic bin A, 10 is the plastic bin B, 11 is the particle outlet, and 12 is the hot air outlet. detailed description The preferred embodiments of the present invention will be described in detail below with reference to the accompanying drawings, so that the advantages and features of the present invention can be more easily understood by those skilled in the art, so as to make a clearer and clearer definition of the protection scope of the present invention. Please refer to Fig. 1, an embodiment of the present invention includes: The described plastic particle dryer includes a dryer base, the dryer base adopts a rectangular parallelepiped structure, the material is made of cast iron material, and the lower end of the dryer base is provided with friction stripes, which make the dryer more stable as a whole. A dryer frame is set on the base of the dryer. The dryer frame is divided into a left bracket and a right bracket. The left bracket and the right bracket are hollow structures. A beam structure is connected between the left and right brackets. A hopper is set in the middle of the beam, a feed port is set at the upper end of the hopper, and a roller is set at the lower end of the hopper. During operation, the plastic particle materials are connected to the hopper. A swing motor is installed in the left bracket. The swing motor is connected to a reducer through a pulley. The reducer is installed in a gear box. A universal drive shaft is installed on the gear box. The universal drive shaft is connected to the drum swing shaft through a swing rod. The other end of the roller swing shaft is connected with the roller as a whole. A sieve hole is set on the outer wall of the drum, and the sieve hole is stirred to make the particles fall from the hopper, so that the particle material falls uniformly. A discharge port is set at the lower end of the hopper, and the discharge port corresponds to the direction of the plastic bin A. A preferred technical solution is that the discharge port of the hopper is equipped with an electronic control valve, which is convenient to control the speed of particle feeding. The particles of the hopper directly fall into the plastic warehouse A. The plastic warehouse A adopts a hexahedral structure. The top of the plastic warehouse A is set to open mode, and the bottom of the plastic warehouse A is equipped with a blower pipe. The blower pipe is connected with a hot blower motor. The warehouse A is connected to the plastic warehouse B through the conveying pipe. The plastic particles enter the plastic warehouse B through the conveying pipe. A hot air outlet is set at the top of the plastic warehouse B. The air is discharged from the hot air outlet. A particle outlet is set at the lower end of the plastic warehouse B. The particles are discharged from the particle outlet. In a preferred technical solution, a collecting bucket is arranged at the particle outlet to facilitate the collection of plastic particles. The above are only the embodiments of the present invention, and do not limit the scope of the present invention. Any equivalent structure or equivalent process transformation made by using the content of the description and drawings of the present invention, or directly or indirectly applied to other related technologies In the same way, all fields are included in the scope of patent protection of the present invention.
|