Method for drying polytetrafluoroethylene suspension resin and manufacturing method for drying system 【Technical Field】 [0001] The present invention relates to the field of drying polymer polymer materials, and relates to a drying method and drying system for polytetrafluoroethylene suspension resin. 【Background technique】 [0002] Polytetrafluoroethylene (Teflon or PTFE), commonly known as "Plastic King", is a polymer compound formed by the polymerization of tetrafluoroethylene, which has excellent chemical stability, corrosion resistance, sealing, high lubricity Viscosity, electrical insulation and good resistance to aging. At present, it has been widely used in aviation, aerospace, atomic energy, electronics, electrical appliances, chemical industry, machinery, construction, textiles, medicine and other industrial sectors, and it has increasingly penetrated into people's daily life. . Tetrafluoroethylene can be obtained by two polymerization processes, suspension and dispersion, and the obtained resin is dried to obtain a powder product. Among them, the drying method of suspended polytetrafluoroethylene resin mainly adopts airflow drying method. [0003] The continuous preparation process of suspension polytetrafluoroethylene powder disclosed in patent CN1184821A proposes a method of air-flow drying. The mashed wet powder is directly sent from a screw feeder to a hot air nozzle for mixing, and then passed through a cone dryer. Cyclone separation is carried out after drying, and the obtained hot material is cooled and separated by cold air at room temperature. This method consumes a lot of air, a large amount of heat is used to heat the air, and the energy consumption is large. At the same time, a large amount of air treatment makes it difficult to guarantee the cleanness of the product. [0004] Patent CN101003593A discloses a method for drying particles in polytetrafluoroethylene suspended resin and proposes a flash drying method, which uses compressed air to enter the flash main engine through decompression, dehumidification, and filtration, and at the same time induces the addition of materials to flash Material drying is realized in the steam drying machine. This method needs to provide a large amount of compressed air, which requires 10 to 20 times the amount of powder, high energy consumption, and high pressure system to increase the cost of drying system equipment; the drying carrier medium is warm air at 20 to 50°C, which has limited drying capacity and is difficult to apply For production systems with high requirements and heavy loads. [0005] Aiming at the problems of large air consumption, large energy and large air clean processing load, and high drying cost, which are common in the current drying method of polytetrafluoroethylene suspension resin, the present invention proposes an energy-saving drying method and system. [Content of the invention] [0006] The technical problem to be solved by the present invention is to provide a polytetrafluoroethylene suspension resin drying method and drying system with low air consumption and energy saving. [0007] In order to solve the above technical problems, the technical solution adopted by the present invention is: a drying method of polytetrafluoroethylene suspension resin, including the following steps: [0008] Step 1. Vibrate and dehydrate the pulverized and washed polytetrafluoroethylene suspension resin slurry to reduce the moisture content of the material on a dry basis to 15% to 20%; [0009] Step 2, centrifugal dewatering the material after vibration dehydration, so that the dry basis moisture content of the material is reduced to 5% ~ 10%; [0010] Step 3, pre-dry the material after centrifugal dewatering, so that the dry basis moisture content of the material is reduced to 0.5% to 1%; [0011] Step 4. Dry the pre-dried material with hot air to reduce the moisture content of the material on a dry basis to 0.05% to 0.1%; [0012] Step 5. Dry the material after hot air drying with cold air to reduce the moisture content of the material on a dry basis to 0.0 2%? 0.04%, that is, dry polytetrafluoroethylene suspension resin. [0013] Another technical solution adopted by the present invention is: a drying system of polytetrafluoroethylene suspension resin, including a vibration unit, a centrifugal unit, a pre-drying unit, a hot air drying unit, and a cold air drying unit connected in sequence; [0014] The vibration unit includes a vibrating screen, the centrifugal unit includes a centrifuge, the pre-drying unit includes a spiral conveying pipe and a steam jacket, the steam jacket is sleeved outside the spiral conveying pipe, and the hot air drying The unit includes a hot air unit, a first Venturi mixer, a hot air drying tube and a first cyclone separator, and the cold air drying unit includes a chiller unit, a second Venturi mixer, a cold air drying tube and a second cyclone separator; [0015] The first Venturi mixer and the second Venturi mixer are provided with a feed inlet, an air inlet and a discharge port, and the first cyclone separator and the second cyclone separator are both provided with feed Mouth, discharge outlet and air outlet; [0016] The outlet of the vibrating screen is connected with the inlet of the Shangxin machine, and the outlet of the Shangxin machine is connected with the inlet of the spiral conveying pipe; [0017] The outlet of the spiral conveying pipe is connected with the inlet of the first venturi mixer, the outlet of the hot air blower unit is connected with the inlet of the first venturi mixer, and the outlet of the first venturi mixer The material port is connected with the inlet of the hot air drying pipe, and the outlet of the hot air drying pipe is connected with the inlet of the first cyclone separator; [0018] The outlet of the first cyclone is connected to the inlet of the second Venturi mixer, the outlet of the chiller unit is connected to the inlet of the second Venturi mixer, and the second The outlet of the Venturi mixer is connected with the inlet of the cold air drying pipe, and the outlet of the cold air drying pipe is connected with the inlet of the second cyclone separator. [0019] The beneficial effect of the present invention is that: in the drying method realized by the polytetrafluoroethylene suspension resin drying system of the present invention, the washed polytetrafluoroethylene suspension resin (a mixture of polytetrafluoroethylene suspension powder and high-purity water) ), after 5 steps of vibration dehydration, centrifugal dehydration, pre-drying, hot air drying and cold air drying, the materials with different water content are divided into 5 levels according to the process by the way of stepped dehydration and drying methods are adopted with the least energy consumption. A dry polytetrafluoroethylene suspension resin powder with a water content of less than 0.04% can be obtained with less energy consumption. The air and energy consumption in the present invention can be reduced by more than 50%, and has the characteristics of low energy consumption, small air cleaning processing load, low drying cost, low product water content and more stable cleanliness. 【Explanation of drawings】 [0020] FIG. 1 is a schematic diagram of the drying system of Example 4 polytetrafluoroethylene suspension resin. [0021] Description of reference signs: [0022] 1, vibrating screen; 11, the first pipe; 2, the centrifuge; 21, the second pipe; 31, spiral conveying pipe; 32, steam jacket; 41, hot air unit; 411, the air inlet of the hot air unit; 412, the first fan; 413, the first medium-efficiency filter module; 414, the steam heating module; 415, the electric heating module; 416, the first high-efficiency filter module; 417, the air outlet of the hot air unit; 42, the first venturi mixing 43. Hot air drying tube; 44. First cyclone separator; 51. Cold air drying unit; 511. Air inlet of chiller unit; 512. Second fan; 513. Second medium efficiency filter module; 514. First refrigeration Dehumidification module; 515, silica gel dehumidification module; 516, the second freezing dehumidification module; 517, the third fan; 518, the second high-efficiency filter module; 519, the air outlet of the chiller unit; 52, the second venturi mixer; 53, Cold air drying tube; 54, the second cyclone separator; 61, the third cyclone separator; 62, the first bag filter; 63, the first induced draft fan; 71, the fourth cyclone separator; 72, the second bag type Dust collector; 73, the second induced draft fan. 【detailed description】 [0023] In order to explain in detail the technical content, the achieved objectives and effects of the present invention, the following description is combined with the embodiments and the accompanying drawings. [0024] The most critical concept of the present invention is to divide materials with different water content into 5 levels according to the process, and use the drying method with the least energy consumption to obtain dry polytetrafluoroethylene with a water content of less than 0.04% with less energy consumption. Ethylene suspension resin powder. [0025] The present invention provides a drying method of polytetrafluoroethylene suspension resin, including the following steps: [0026] Step 1. Vibrate and dehydrate the pulverized and washed polytetrafluoroethylene suspension resin slurry to reduce the dry basis moisture content of the material to 15% to 20%; [0027] Step 2. Centrifugal dewatering the material after vibration dehydration, so that the dry basis moisture content of the material is reduced to 5% ~ 10%; [0028] Step 3, pre-dry the material after centrifugal dewatering, so that the dry basis moisture content of the material is reduced to 0.5% to 1%; [0029] Step 4. The pre-dried material is dried with hot air, so that the dry basis moisture content of the material is reduced to 0.05% to 0.1%; [0030] Step 5. Dry the material after hot air drying with cold air to reduce the moisture content of the material on a dry basis to 0.0 2%? 0.04%, that is, dry polytetrafluoroethylene suspension resin. [0031] It can be seen from the above description that the beneficial effects of the present invention are: the pulverized and washed polytetrafluoroethylene suspension resin (a mixture of polytetrafluoroethylene suspension powder and high-purity water) is subjected to vibration dehydration, centrifugal dehydration, and pre-drying , 5 steps of hot air drying and cold air drying, the material with different water content is divided into 5 steps according to the process by the way of step dehydration drying, and the drying method with the least energy consumption is adopted, and the water content is less than 0.04 with less energy consumption. % Dry polytetrafluoroethylene suspension resin powder. The air and energy consumption in the present invention can be reduced by more than 50%, and has the characteristics of low energy consumption, small air cleaning processing load, low drying cost, low product water content and more stable cleanliness. [0032] Further, it also includes the cyclone separation of the material after the hot air drying and then the cold air drying.
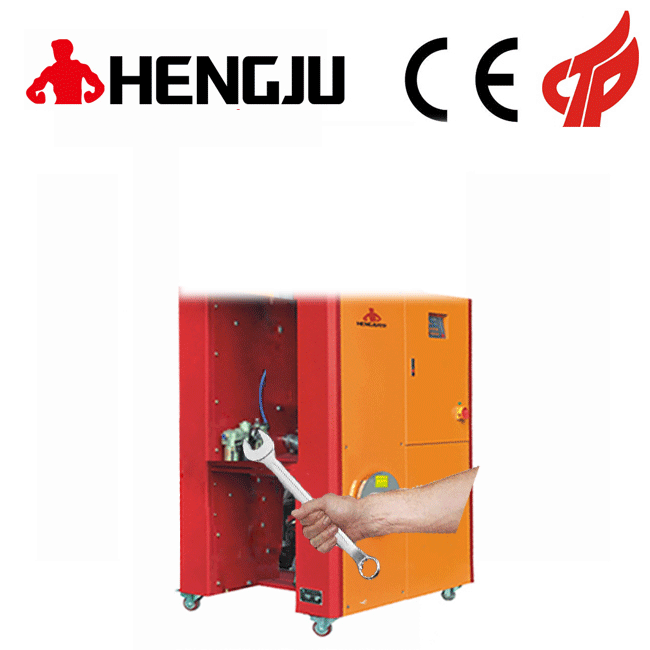 [0033] It can be seen from the above description that cyclone separation is carried out after the hot air drying, which can separate the hot air from the material, avoid affecting the cold air drying of the material and save energy. [0034] Further, in step 2, a centrifuge is used for centrifugal dehydration, and the process parameters are: rotational speed 2000-4000r/min. [0035] It can be seen from the above description that the centrifuge uses a rotation speed of 2000 to 4000 r/min for material dehydration, which can shorten the dehydration time. [0036] Further, the pre-drying in step 3 adopts steam drying and screw conveying, and its process parameters are: drying time 0.5-2min, -HS*0.51.0MPa. [0037] It can be seen from the above description that the pre-drying of materials adopts steam drying and spiral conveying methods, and when the steam pressure of the steam jacket is 0.5 to 1.0 MPa, it is dried in the spiral conveying pipe for 0.5 to 2 minutes, which can consume more Dry the material with moisture content of 5% to 10% on dry basis to 0.5% to 1% of moisture content on dry basis with less heat energy. [0038] Further, the process parameters of hot air drying in step 4 are: the air volume is 2 to 5 kg/kg of material, and the temperature is 150 to 250V. [0039] It can be seen from the above description that the pre-dried materials are dried with hot air under the conditions of air volume of 2-5kg/kg material and temperature of 150-250°C, which can minimize hot air consumption and save energy. [0040] Further, the process parameters of cold air drying in step 5 are: air volume 2 ~ 5kg/kg material, temperature 5 ~ 20 °C, dew point -40 ~ -20 °C ο
|