|
TPU Dehumidifying dryer parameter
TPU Dehumidifying dryer
Plastic material |
Dryer |
Density (kg/dm3) |
Drying time(h) |
Drying temperature (℃) |
Atmospheric flow(m3/kg) |
Moulding moisture content(%) |
Initial moisture contnt(%) |
TPU |
√ |
0.75 |
2-3 |
70-100 |
2 |
<0.02 |
- |
|
TPU Dehumidifying dryer Equipment principle
TPU desiccant dryer has the following four major performance characteristics: 1. Simple and flexible operation The TPU desiccant dryer adopts a brand-new microprocessor controller, which is easy to operate. The indicator light on the operation panel indicates the working status of the dryer. Each drying barrel is equipped with a thermal insulation layer and an independent temperature controller, so that different raw material drying temperatures can be flexibly set in the application of a dryer with multiple drying barrels. The specially designed drying barrel structure ensures uniform drying of raw materials and uniform discharge. 2. Flexibility and efficiency The TPU molecular sieve dehumidification dryer has two molecular sieve barrels to ensure the continuity of the drying process. The dryer can be connected to multiple barrels at the same time, thus ensuring the greater possible flexibility and continuity of the production process. When replacing the raw materials in one drying barrel, the other barrels can still dry the raw materials normally, effectively avoiding the problem of possible output reduction due to material change. 3. Humanized design The drying barrel of the TPU desiccant dryer is equipped with a large-size cleaning door for easy cleaning. Modular combination of dryer and drying barrel, users only need to change the number or specifications of drying barrels to easily adapt to changes in future production requirements. In addition, the modular and compact design of the desiccant dryer greatly reduces the area occupied by the dryer and drying barrel. Users can also install casters on the drying barrel and drying barrel to move freely according to actual production needs. 4. Stable and reliable The TPU dehumidification dryer has the characteristics of sturdiness and high efficiency. The stable control mode and reliable system ensure the excellent performance of the dehumidification dryer, making the production work more stable and reliable, saving energy and electricity, and reducing maintenance costs. The above content is about the performance characteristics of TPU desiccant dryer, I believe everyone has already understood. TPU desiccant dryer has simple operation, flexible setting, high drying efficiency, good dehumidification effect and low cost. It is developed and produced for TPU plastic and is an important equipment indispensable for TPU raw material processingLet's first talk about ordinary dryers. Ordinary dryers use electric heating to heat hot air to dry materials in the space at a high temperature, and the purpose is to evaporate water from the materials. The incoming air heated by the electric heating is the air in the environment. In dry weather and humid weather, the moisture content in the air is different. Therefore, when the weather is wet, incomplete drying of the material will occur. Because electric heating must first heat the incoming air, but the incoming air contains high moisture, how can the TPO material be dried thoroughly? (Mainly reflected in materials with high moisture absorption rate, such as nylon). For this reason, the desiccant dryer came into being. In view of the above situation, firstly, the ambient air is drawn in to remove the moisture in the air at a low dew point, and then relatively dry air is used to heat the material into the dryer to dry the material. Therefore, the difference between these two dryers is that the moisture content of the inlet air used for drying is different. One has processed the inlet air moisture, and the other has not processed the inlet air moisture. TPU Dehumidifying dryer can dry to a moisture content below 0.02%, and solves the shortcomings of poor transparency, sprue sticking, bubbles, silver bars, cracks, poor dimensional stability, internal stress, and insufficient product physical strength.
Dehumidification and drying feeding equipment series are composed of: non-heat dehumidification dryer, heat preservation type drying barrel and all stainless steel suction machine. The suction machine can transport the raw materials from the drying barrel to the forming machine, and can also transport the raw materials from the storage barrel to the drying barrel. According to customer needs, a kind of raw material can be delivered to two molding machines, vacuum motors and safety filter dust collectors are installed inside the machine. According to the production needs of different products, we can provide a powder-removing suction machine to separate the powder in the raw material and capture it. This device has a compact structure and is suitable for the production of precision injection products using engineering plastics such as connectors, precision gears, mobile phone communications, digital cameras and product size requirements, so that the moisture content of the raw materials after wet and dry is low and stable, which can meet strict requirements Technical and quality requirements.
Most engineering plastics are hygroscopic. When the plastic is taken out from the moisture-proof sealed packaging bag and exposed to the atmosphere, it will begin to absorb moisture from the atmosphere.
If it is a conventional hot-air barrel dryer, it is Humid external air can dry the plastic, so it cannot prevent the plastic from continuing to absorb moisture.
1. The internal circulation of the dehumidifier: through the operation of the compressor → discharge high-temperature and high-pressure gas through the exhaust port → enter the condenser for cooling → become a low-temperature and high-pressure gas → pass through the capillary tube → become a low-temperature and low-pressure liquid → evaporate and suck through the evaporator Heat → until the compressor becomes a low-temperature and low-pressure gas. So it goes back and forth.
2. The external circulation of the dehumidifier: under normal startup → through the operation of the fan → moist air is sucked in from the air inlet → passes through the evaporator → the evaporator absorbs the moisture in the air on the aluminum sheet → becomes dry air → Pass through the condenser to dissipate heat → blow out from the air outlet.
|
TPU Dehumidifying dryer application
TPU DehumidifyiThe desiccant dryer originated in Sweden. Its drying principle is to use a motor to drive the rotor to slowly rotate. The silica gel coated on the rotor is used to physically adsorb the moisture in the air on the porous synthetic silica gel. In the regeneration zone of the runner, the water vapor adsorbed in the silica gel holes is heated and vaporized to the inlet of the AC heat exchanger to form high temperature and high humidity air, and then pass through the heat exchanger that has been cooled by the indoor cold and humid air. The difference is that the condensed water is discharged, and the cycle works in this way to achieve the purpose of air drying.ng dryer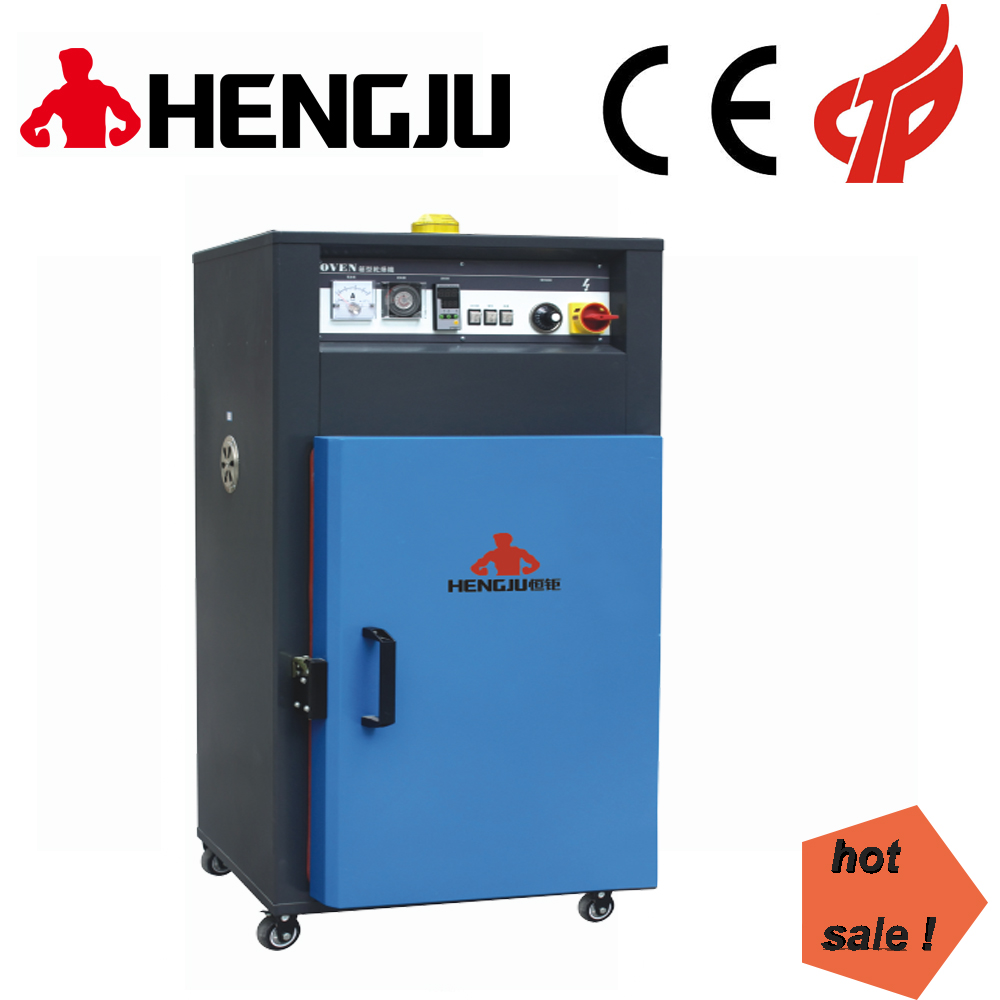 I believe everyone is familiar with TPU plastic. It has applications in automotive parts, mechanical parts, rubber, rubber, wires and cables, daily chemicals, shoe materials and other fields, covering almost all industries. Due to the high water absorption of TPU itself, TPU plastic processing requires particularly high moisture content. It is necessary to use a TPU dehumidifying dryer to dehumidify and dry it to ensure that the moisture content of the raw material is below 100PPM, and does not agglomerate due to high temperature. quality. Next, Gaosi will introduce the performance characteristics of TPU desiccant dryer in detail. With the widespread use of engineering plastics, Dehumidifying dryers have gradually replaced traditional hot air dryers.
This is a device used to dehumidifying plastic resin to achieve drying. For example,
POM,ABS,TPE,PAL,ABS,CAB,EVA(2),EVOH,LM(4),LCP,PA11,PA6.46.6,PAI,PAR,PBT,
PC,PC/ABS,PC/PBT,PE.HDEPE,LDPE black3%,PE.HDEPE.LDPE black40%,PEEK,PE(1),
PEN,PES,PET,PETG,PI,PMMA,POM,PP,PPO,PPS,PS,[GPPS.EPS.HIPS],PSU,PIT,PUR,
PVC,SAN,SB,TPE,TPE,TPO,TPU,
Dehumidifier dryerand other plastic resins must be dehumidified and dried during the production process to improve the quality of the finished product.
TPU Dehumidifying dryer series are mainly designed for high-efficiency dehumidification of engineering plastics with strong hygroscopicity. Using the honeycomb runner with ceramic fiber as the base material, which represents the highest technological achievements of today, as the core component, the dry air provided can easily reach -40℃ dew point, and ideally it can reach -50℃ or even lower dew point , And the dew point temperature is stable, ensuring the high quality and stability of the molded plastic products. The whole series adopts P.LD. temperature control system as standard equipment; also provides PLC control with LCD touch-sensitive human-machine interface and can monitor the dehumidification effect of the machine Dew point meter is optional, the maximum drying air volume of this product can reach 3000m3/hr. The plastic before molding must be dried to an orientation ratio of less than 0.02%, which is completely bad, sprue adhesion, burrs, bubbles, silver bars, flow marks, cracks, dimensional stability and internal stress. Product defects (for example, insufficient physical properties and strength) are caused by sufficient dehumidification of the plastic before molding. Especially for PET, PBT, PA, PC and other high water absorption plastics, drying equipment with an ultra-low dew point of -40°C is required.
TPU Dehumidifying dryer can be dried to a volume ratio of less than 0.02%, which solves the shortcomings of short circuit, gate adhesion, bubbles, silver bars, cracks, poor dimensional stability, internal stress and insufficient physical strength of the product. There are a lot more.
Mainly used in plastic products, automobiles, optical discs, experiments, communications, optics, etc.; the rotary honeycomb can reach a low dew point of zero bai for dehumidification and drying at -40°C. In the case of enhanced configuration, the dehumidification dew point can be as high as -50°C. It is a choice for high-precision industries.
TPU Dehumidifying dryer Precautions
Operation process of desiccant dryer: 1, please make sure the installation and adjustment have been completed; 2, please turn on the power switch of the control box and the dehumidifier panel; 3. When the temperature rises to the set temperature, check whether the temperature of the lower part is consistent; 4. The temperature indicator of the barrel can be inspected at any time, and the fault can be checked and repaired; 5. Keep the barrel full at any time during production; 6. When the raw materials are dried for a specified time, they can be produced; 7. Before stopping. First close the feeding plate and drain the raw materials underneath, then close the feeding system; 8. The standard temperature of the baking material is based on the following "plastic raw material baking temperature and time as the setting standard".
|
|
|