|
TPO polymer dryer parameter
TPO Dehumidifying dryer /td>
Plastic material |
Dryer |
Density (kg/dm3) |
Drying time(h) |
Drying temperature (℃) |
Atmospheric flow(m3/kg) |
Moulding moisture content(%) |
Initial moisture contnt(%) |
TPO |
√ |
0.55 |
3 |
70-90 |
2 |
- |
- |
|
TPO polymer dryer Equipment principle
TPO Dehumidifying dryer 1. It integrates three functions of dehumidification, drying, and bai two-stage feeding; 2. The dehumidification part is equipped with a wheel device, which can provide stable and low dew point air, and the dew point can reach below -40℃; 3. The stainless steel double-layer heat preservation drying barrel adopts the design of lower blowing pipe to make the raw materials evenly dry and effectively prevent heat loss; 4. The feeding system is equipped with a shut-off valve to ensure that there is no residual raw material in the material pipe; 5. The closed feeding system can prevent the raw materials from being polluted or re-moisture; 6. The optical grade GCD-OP model is matched with a boiling electric eye hopper, which can remove the fine powder in the raw material, and can avoid pollution during the molding of optical grade products. Point generation; 7. The optical-grade GCD-OP model system is equipped with high-precision and high-efficiency filters, which can effectively filter dust ions up to 0.3μm, and the filtration rate is up to 99.9%; 8. PLC control with LCD touch-sensitive man-machine interface can be purchased, the operation is centralized and convenient, and the whole machine can be controlled to run automatically; 9. Dew point detection device can be purchased; can dry to a moisture content below 0.02%, and solves the shortcomings of poor transparency, sprue sticking, bubbles, silver bars, cracks, poor dimensional stability, internal stress, and insufficient product physical strength.
Dehumidification and drying feeding equipment series are composed of: non-heat dehumidification dryer, heat preservation type drying barrel and all stainless steel suction machine. The suction machine can transport the raw materials from the drying barrel to the forming machine, and can also transport the raw materials from the storage barrel to the drying barrel. According to customer needs, a kind of raw material can be delivered to two molding machines, vacuum motors and safety filter dust collectors are installed inside the machine. According to the production needs of different products, we can provide a powder-removing suction machine to separate the powder in the raw material and capture it. This device has a compact structure and is suitable for the production of precision injection products using engineering plastics such as connectors, precision gears, mobile phone communications, digital cameras and product size requirements, so that the moisture content of the raw materials after wet and dry is low and stable, which can meet strict requirements Technical and quality requirements.
Most engineering plastics are hygroscopic. When the plastic is taken out from the moisture-proof sealed packaging bag and exposed to the atmosphere, it will begin to absorb moisture from the atmosphere.
If it is a conventional hot-air barrel dryer, it is Humid external air can dry the plastic, so it cannot prevent the plastic from continuing to absorb moisture.
1. The internal circulation of the dehumidifier: through the operation of the compressor → discharge high-temperature and high-pressure gas through the exhaust port → enter the condenser for cooling → become a low-temperature and high-pressure gas → pass through the capillary tube → become a low-temperature and low-pressure liquid → evaporate and suck through the evaporator Heat → until the compressor becomes a low-temperature and low-pressure gas. So it goes back and forth.
2. The external circulation of the dehumidifier: under normal startup → through the operation of the fan → moist air is sucked in from the air inlet → passes through the evaporator → the evaporator absorbs the moisture in the air on the aluminum sheet → becomes dry air → Pass through the condenser to dissipate heat → blow out from the air outlet.
|
TPO polymer dryer application
TPO Dehumidifying dryer I believe everyone is familiar with TPU plastic. It has applications in automotive parts, mechanical parts, rubber, rubber, wires and cables, daily chemicals, shoe materials and other fields, covering almost all industries. Due to the high water absorption of TPU itself, TPU plastic processing requires particularly high moisture content. It is necessary to use a TPU dehumidifying dryer to dehumidify and dry it to ensure that the moisture content of the raw material is below 100PPM, and does not agglomerate due to high temperature. quality. Next, Gaosi will introduce the performance characteristics of TPU desiccant dryer in detail.
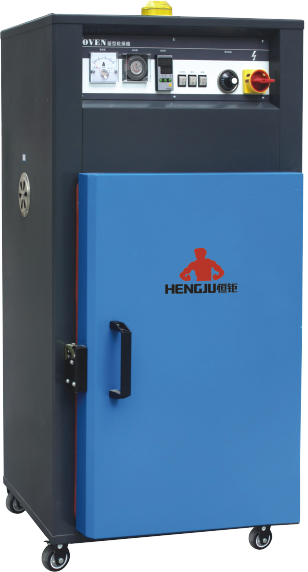 With the widespread use of engineering plastics, Dehumidifying dryers have gradually replaced traditional hot air dryers.
This is a device used to dehumidifying plastic resin to achieve drying. For example,
POM,ABS,TPE,PAL,ABS,CAB,EVA(2),EVOH,LM(4),LCP,PA11,PA6.46.6,PAI,PAR,PBT,
PC,PC/ABS,PC/PBT,PE.HDEPE,LDPE black3%,PE.HDEPE.LDPE black40%,PEEK,PE(1),
PEN,PES,PET,PETG,PI,PMMA,POM,PP,PPO,PPS,PS,[GPPS.EPS.HIPS],PSU,PIT,PUR,
PVC,SAN,SB,TPE,TPE,TPO,TPU,
Dehumidifier dryerand other plastic resins must be dehumidified and dried during the production process to improve the quality of the finished product.
TPO polymer dryer series are mainly designed for high-efficiency dehumidification of engineering plastics with strong hygroscopicity. Using the honeycomb runner with ceramic fiber as the base material, which represents the highest technological achievements of today, as the core component, the dry air provided can easily reach -40℃ dew point, and ideally it can reach -50℃ or even lower dew point , And the dew point temperature is stable, ensuring the high quality and stability of the molded plastic products. The whole series adopts P.LD. temperature control system as standard equipment; also provides PLC control with LCD touch-sensitive human-machine interface and can monitor the dehumidification effect of the machine Dew point meter is optional, the maximum drying air volume of this product can reach 3000m3/hr. The plastic before molding must be dried to an orientation ratio of less than 0.02%, which is completely bad, sprue adhesion, burrs, bubbles, silver bars, flow marks, cracks, dimensional stability and internal stress. Product defects (for example, insufficient physical properties and strength) are caused by sufficient dehumidification of the plastic before molding. Especially for PET, PBT, PA, PC and other high water absorption plastics, drying equipment with an ultra-low dew point of -40°C is required.
TPO polymer dryer can be dried to a volume ratio of less than 0.02%, which solves the shortcomings of short circuit, gate adhesion, bubbles, silver bars, cracks, poor dimensional stability, internal stress and insufficient physical strength of the product. There are a lot more.
Mainly used in plastic products, automobiles, optical discs, experiments, communications, optics, etc.; the rotary honeycomb can reach a low dew point of zero bai for dehumidification and drying at -40°C. In the case of enhanced configuration, the dehumidification dew point can be as high as -50°C. It is a choice for high-precision industries.
TPO polymer dryer Precautions
TPO Dehumidifying dryer
|
|
|