Resin Dehumidifying Dryer Details description |
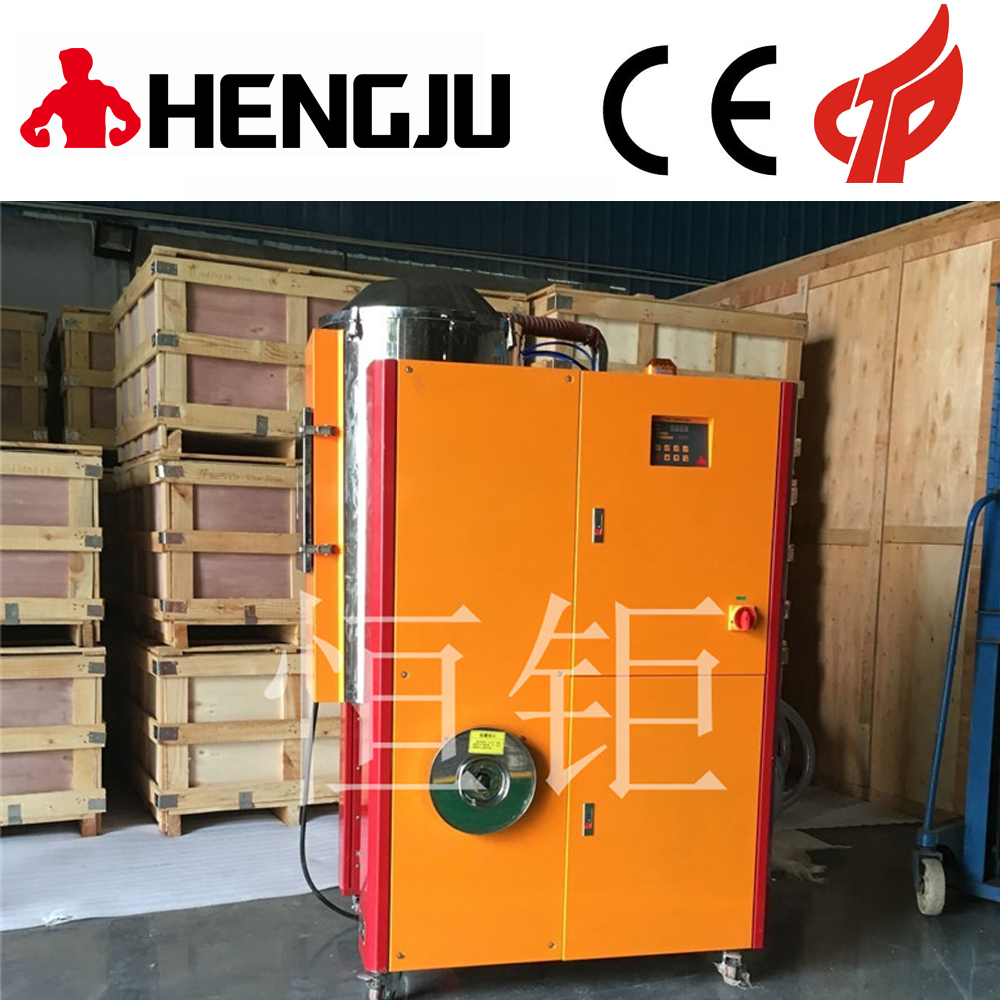 |
product name:Resin Dehumidifying Dryer |
release time:2020-09-16 |
Numbering:Resin Dehumidifying Dryer -001 |
Brand:wto-btb |
Price:¥By function |
weight :By function |
unit weight:Kg/set |
manufacturer:wto-btb |
patent:wto-btb |
Producing country:china |
simple description:Resin Dehumidifying Dryer, Plastic Dehumidifying Dryer,Dehumidifying Dryer |
Product alias:Resin Dehumidifying Dryer, Plastic Dehumidifying Dryer,Dehumidifying Dryer |
|
Resin Dehumidifying Dryer Product introduction |
|
Resin Dehumidifying Dryer parameter
Resin Dehumidifying Dryer, Plastic Dehumidifying Dryer,Dehumidifying Dryer
Resin Dehumidifying Dryer model |
Resin Dehumidifying Dryer Loading(kg) |
Dry electric heating(KW) |
Resin Dehumidifying Dryer Fan(W) |
Resin Dehumidifying Dryer Dimensions |
Resin Dehumidifying Dryer Applicable molding machine |
HD-25 |
25 |
3 |
100 |
967*715*385 |
3 oz
|
HD-50 |
50 |
3.9 |
140 |
1150*810*449 |
5-8 oz
|
HD-100 |
100 |
6.2 |
350 |
1395*1010*557 |
10-30 oz
|
HD-150 |
150 |
7 |
750 |
1515*1200*660 |
30 oz
|
HD-200 |
200 |
11 |
750 |
1670*1160*752 |
60 oz
|
HD-300 |
300 |
18 |
1100 |
1890*1550*870 |
60 oz
|
HD-400 |
400 |
20 |
1100 |
2043*1550*870 |
60 oz
|
HD-600 |
600 |
25 |
1100 |
2543*1550*870 |
60 oz
|
|
Resin Dehumidifying Dryer Equipment principle
Resin Dehumidifying Dryer, Plastic Dehumidifying Dryer,Dehumidifying Dryer Working principle of dehumidifying plastic dryer: The amount of water vapor in compressed air is determined by the temperature of the compressed air: while keeping the compressed air pressure basically unchanged, lowering the temperature of the compressed air can reduce the water vapor content in the compressed air, and the excess water vapor will condense Into liquid. The freeze dryer uses this principle to use refrigeration technology to dry compressed air. Therefore, the refrigeration dryer has a refrigeration system. The refrigeration system of the freeze dryer belongs to compression refrigeration, which consists of four basic components, including a refrigeration compressor, a condenser, an evaporator, and an expansion valve. They are connected in turn by pipes to form a closed system. The refrigerant continuously circulates in the system, changes its state and exchanges heat with the compressed air and cooling medium. The dryer vaporizes and escapes the moisture in the material (generally refers to moisture or other volatile liquid components) by heating to obtain a solid material with a specified moisture content. The purpose of drying is for material use or further processing. 1. The dehumidification runner is made of ceramic fiber paper with a temperature resistance of more than 500℃. After the honeycomb runner is made by the molding machine, the silica gel is then coated between the ceramic fibers. Therefore, the dehumidification runner will not burn and Deliquescence and other issues. Because its dehumidification function uses physical rather than chemical effects, it will not produce any harmful chemical substances. 2. The dehumidification principle of the rotary dehumidifier is to use the silica gel coated on the runner to physically adsorb the moisture in the air on the porous synthetic silica gel, and then in the regeneration zone of the runner, it will be adsorbed on the silica gel. The water vapor in the hole is heated and vaporized to the inlet of the AC heat exchanger to form high temperature and high humidity air. When it passes through the heat exchanger that has been cooled by the indoor cold and humid air, the condensation water is discharged due to the difference in dew point. Features of Dehumidifying Plastic Dryer: ◆High thermal efficiency, greatly shortening the drying time. ◆Silent fan, with oblique windows on the base, you can directly observe the inside. ◆The curved design of the electric heating cylinder avoids burning caused by the accumulation of raw material dust on the bottom of the barrel. ◆Adopt digital display thermostat to control temperature. ◆The material contact surface is all stainless steel design to ensure the material. ◆Dust isolation and silent fan can isolate dust and ensure raw materials. ◆The barrel base is designed with a viewing window to directly observe the internal working conditions. ◆The bend-shaped design of the heating tube of the up-blowing dryer avoids damage to the heating tube caused by the material falling into the barrel. ◆Using a high-performance hot air diffusion device that evenly disperses hot air to keep the plastic drying temperature uniform and increase drying efficiency. ◆Each model can be equipped with timing device. can dry to a moisture content below 0.02%, and solves the shortcomings of poor transparency, sprue sticking, bubbles, silver bars, cracks, poor dimensional stability, internal stress, and insufficient product physical strength.
Dehumidification and drying feeding equipment series are composed of: non-heat dehumidification dryer, heat preservation type drying barrel and all stainless steel suction machine. The suction machine can transport the raw materials from the drying barrel to the forming machine, and can also transport the raw materials from the storage barrel to the drying barrel. According to customer needs, a kind of raw material can be delivered to two molding machines, vacuum motors and safety filter dust collectors are installed inside the machine. According to the production needs of different products, we can provide a powder-removing suction machine to separate the powder in the raw material and capture it. This device has a compact structure and is suitable for the production of precision injection products using engineering plastics such as connectors, precision gears, mobile phone communications, digital cameras and product size requirements, so that the moisture content of the raw materials after wet and dry is low and stable, which can meet strict requirements Technical and quality requirements.
Most engineering plastics are hygroscopic. When the plastic is taken out from the moisture-proof sealed packaging bag and exposed to the atmosphere, it will begin to absorb moisture from the atmosphere.
If it is a conventional hot-air barrel dryer, it is Humid external air can dry the plastic, so it cannot prevent the plastic from continuing to absorb moisture.
1. The internal circulation of the dehumidifier: through the operation of the compressor → discharge high-temperature and high-pressure gas through the exhaust port → enter the condenser for cooling → become a low-temperature and high-pressure gas → pass through the capillary tube → become a low-temperature and low-pressure liquid → evaporate and suck through the evaporator Heat → until the compressor becomes a low-temperature and low-pressure gas. So it goes back and forth.
2. The external circulation of the dehumidifier: under normal startup → through the operation of the fan → moist air is sucked in from the air inlet → passes through the evaporator → the evaporator absorbs the moisture in the air on the aluminum sheet → becomes dry air → Pass through the condenser to dissipate heat → blow out from the air outlet.
|
Resin Dehumidifying Dryer application
Resin Dehumidifying Dryer In the plastics processing industry, products appear shrinkage, silver streaks, bubbles, cracks, flow marks, poor transparency, etc. The main reason for these poor quality is that the plastics are not sufficiently dried before they are formed. Engineering plastics such as : PA, PET, PC, PBT, CA and other highly hygroscopic raw materials, due to the penetration of water into the plastic particles, the traditional hot air dryer can not make it completely dry. Practice has proved that reducing the dew point of the drying wind to below -40°C while controlling the heat to blow it over the surface of the moisture-containing plastic particles can reduce its moisture content to below 0.02% before molding. The three-in-one dehumidification dryer is airtight. The circulatory system fully dehumidifies and heats the air, and the dry air quickly completely separates the moisture in the plastic particles to achieve the effect of dehumidification and drying. The plastic dryer is the most effective and economical scale for drying plastic raw materials. It can dry raw materials placed for packaging, transportation or recycling.
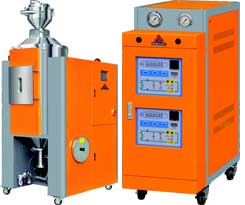 The hopper is made of stainless steel, with the functions of "blowing down hot air" and "cyclone exhaust", as well as double-layer insulation barrels. It is particularly suitable for use with a dehumidifier as raw material for drying engineering plastics. 1. Using P.I.D temperature control system, precise temperature control;
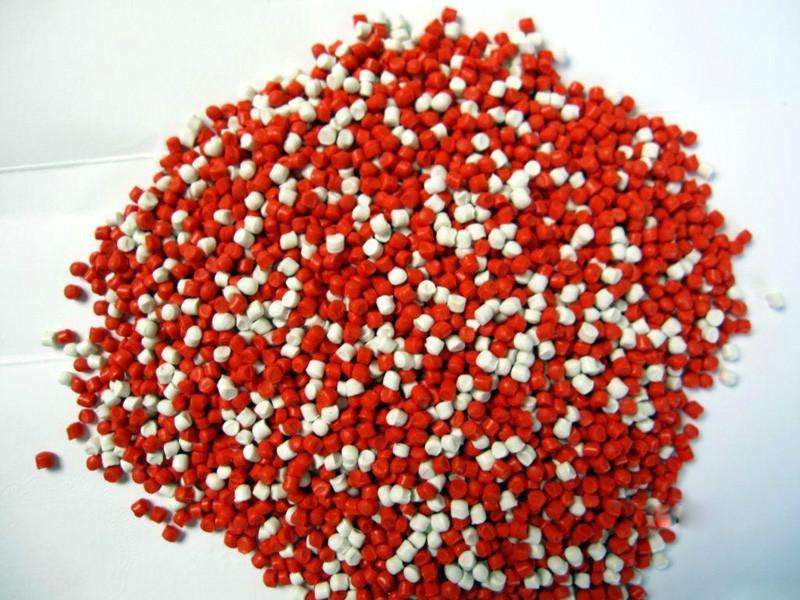 2. The unique downward blowing air duct design can evenly disperse the hot air, keep the plastic dry, keep the temperature stable, and improve the drying efficiency; 3. Stainless steel double-layer insulation material barrel with sight window; 4. Widely available GHD-40U and above models are equipped with an openable sight door; 5. Thermal overload protection device, safe and reliable; 6. Novel appearance and bright appearance; The air blown by the drying fan becomes high-temperature dry air after drying and electric heating. Through the unique lower blowing pipe design, the hot air is evenly dispersed in the insulation barrel to dry the raw materials; a hot air recovery device is optional, and the air blown out is filtered and then dried The wind blows out, forming a closed loop. With the widespread use of engineering plastics, Dehumidifying dryers have gradually replaced traditional hot air dryers.
This is a device used to dehumidifying plastic resin to achieve drying. For example,
POM,ABS,TPE,PAL,ABS,CAB,EVA(2),EVOH,LM(4),LCP,PA11,PA6.46.6,PAI,PAR,PBT,
PC,PC/ABS,PC/PBT,PE.HDEPE,LDPE black3%,PE.HDEPE.LDPE black40%,PEEK,PE(1),
PEN,PES,PET,PETG,PI,PMMA,POM,PP,PPO,PPS,PS,[GPPS.EPS.HIPS],PSU,PIT,PUR,
PVC,SAN,SB,TPE,TPE,TPO,TPU,
Dehumidifier dryerand other plastic resins must be dehumidified and dried during the production process to improve the quality of the finished product.
Resin Dehumidifying Dryer series are mainly designed for high-efficiency dehumidification of engineering plastics with strong hygroscopicity. Using the honeycomb runner with ceramic fiber as the base material, which represents the highest technological achievements of today, as the core component, the dry air provided can easily reach -40℃ dew point, and ideally it can reach -50℃ or even lower dew point , And the dew point temperature is stable, ensuring the high quality and stability of the molded plastic products. The whole series adopts P.LD. temperature control system as standard equipment; also provides PLC control with LCD touch-sensitive human-machine interface and can monitor the dehumidification effect of the machine Dew point meter is optional, the maximum drying air volume of this product can reach 3000m3/hr. The plastic before molding must be dried to an orientation ratio of less than 0.02%, which is completely bad, sprue adhesion, burrs, bubbles, silver bars, flow marks, cracks, dimensional stability and internal stress. Product defects (for example, insufficient physical properties and strength) are caused by sufficient dehumidification of the plastic before molding. Especially for PET, PBT, PA, PC and other high water absorption plastics, drying equipment with an ultra-low dew point of -40°C is required.
Resin Dehumidifying Dryer can be dried to a volume ratio of less than 0.02%, which solves the shortcomings of short circuit, gate adhesion, bubbles, silver bars, cracks, poor dimensional stability, internal stress and insufficient physical strength of the product. There are a lot more.
Mainly used in plastic products, automobiles, optical discs, experiments, communications, optics, etc.; the rotary honeycomb can reach a low dew point of zero bai for dehumidification and drying at -40°C. In the case of enhanced configuration, the dehumidification dew point can be as high as -50°C. It is a choice for high-precision industries.
Resin Dehumidifying Dryer Precautions
Resin Dehumidifying Dryer, plastic Dehumidifying Dryer,Dehumidifying Dryer The factors affecting the drying effect are: Drying temperature: Heat is the key to open the force between water molecules and hygroscopic polymer. When the temperature is higher than a certain temperature, the attraction between water molecules and polymer chains will be greatly reduced, and the water vapor will be taken away by the dry air. Dew point: In the dryer, the humid air is first removed to make it contain very low residual moisture (dew point). Then, heat the air to lower its relative humidity. At this time, the vapor pressure of dry air is low. By heating, the water molecules inside the particles get rid of the binding force and diffuse to the air around the particles. Time: In the air around the particles, it takes a certain time for the absorption of heat and the diffusion of water molecules to the surface of the particles. Therefore, the resin supplier should specify the time it takes for a material to be effectively dried at the appropriate temperature and dew point. Airflow: The dry hot air transfers heat to the particles in the drying silo, removes moisture on the surface of the particles, and then sends the moisture back to the dryer. Therefore, there must be enough airflow to heat the resin to the drying temperature and maintain this temperature for a certain period of time. When the problem of poor drying occurs, the problem should be found from the following three aspects: 1. Condition of the dryer When inspecting the dryer, pay special attention to the air filter and hose. A clogged filter or a squashed hose will reduce airflow, thereby affecting the operation of the dryer; A damaged filter will contaminate the desiccant and inhibit its moisture absorption capacity; a broken hose may introduce moist ambient air into the dry air flow, causing the desiccant to prematurely absorb moisture and high dew point; hoses and desiccants with poor insulation The bin also affects the drying temperature. 2. Dry air circuit In the drying air circuit, the drying temperature should be detected at the entrance of the silo to compensate for the heat loss of the dryer in the hose. The low air temperature at the inlet of the silo may be due to improper adjustment of the controller and lack of insulation, or malfunction of the heater element, heater contactor, thermocouple or controller. In addition, it is also important to monitor the drying temperature at various locations during the entire drying process and observe temperature fluctuations when the desiccant is replaced. If the material is not properly dried after coming out of the dryer, check whether the drying silo has enough space to provide sufficient and effective drying time. The effective drying time refers to the time the particles are actually exposed to the appropriate drying temperature and dew point. If the particles stay in the silo for insufficient time, they will not get proper drying. Therefore, attention should be paid to the size and shape of pellets or crushed materials, as they will affect the bulk density and residence time of the dried materials. A kinked hose or a clogged filter can restrict airflow and affect the performance of the dryer. Therefore, if you check the dryer and find no such problems, you cannot judge whether the airflow is sufficient. Here, there is a quick, simple and accurate method to detect whether the airflow of the dryer is sufficient, that is, to measure the vertical temperature curve of the material in the drying silo. Assume that the drying time recommended by the material supplier is 4h and the processing capacity is 100lb/h (1lb=0.4536Kg). To determine whether the airflow of the dryer is sufficient, you can measure the temperature curve in the drying silo. Here, pay special attention to the temperature at 4h (400lb). If the temperature at the 400lb material level in the dry silo reaches the set value, then the air flow can be considered sufficient. If only the material at 1h, 2h or 3h in the drying silo is fully heated, it means that the air flow cannot complete the heating and drying of the material at the predetermined yield. Insufficient heating may indicate that the drying silo is too small for this rate of production, or the airflow is restricted due to clogged filters or damaged hoses. Excessive air volume can cause problems, which not only wastes energy, but also causes high return air temperature and destroys the performance of the desiccant. The return air filter can prevent the filamentous material from polluting the desiccant and affect its moisture absorption performance. These filters must be kept clean to ensure adequate airflow. When the dry air comes out of the top of the dryer, most of the heat has been released. When the desiccant temperature is in the range of 120oF to 150oF, most dryers can work efficiently. If the return air overheats the desiccant, it will reduce its ability to absorb moisture in the dry air. Always check the return air temperature of the dryer. When the return air temperature is high, it may indicate that the size of the dryer is too large for the productivity, or the temperature of the material entering the drying silo is high. For example, PET has crystallized before drying, or only certain materials (such as PET ) The drying temperature is higher than the normal temperature range. In order to prevent the return air temperature from becoming high, as long as a heat exchanger is installed on the return air path, the desiccant can effectively remove the moisture in the dry air. 3. Regeneration and cooling of desiccant The moisture absorption capacity of the desiccant is limited, so the moisture absorbed by it must be removed by regeneration. The process is: when the ambient air is sucked in, it enters the blower through a filter, and then is sent to a set of heaters. The heated air passes through the desiccant bed. When the temperature of the desiccant rises, the adsorbed moisture is released. When the hot air is saturated with water vapor, it is discharged into the atmosphere. The high-temperature regenerated desiccant must be cooled before returning to the drying loop to restore the moisture absorption function of the desiccant. Dew point readings can help find some problems, so the dew point of dry air should be monitored throughout the drying process. The dew point reading during normal operation of the dryer should be a straight line in the range of 20oF to 50oF. Of course, small fluctuations caused by replacing the desiccant are normal. If the dryer is operating normally, the dew point at the dry air inlet should be at least 30oF lower than the dew point at the return air outlet. On the other hand, after the desiccant is replaced, the dew point immediately peaks, indicating that the desiccant is not sufficiently cooled before being put in, making it unable to absorb moisture well. After cooling, the dew point of the desiccant will drop to the normal standard. If the desiccant is not properly cooled, it will cause the temperature to peak, and the sudden temperature change will reduce the desiccant's ability to dry heat-sensitive materials such as ionomers, amorphous polyester and certain nylon grades. If the dew point reading is normal after the desiccant bed is replaced, but the dew point rises rapidly before the end of the drying cycle of the desiccant, it means that the ambient air may have entered the closed air circuit, causing the desiccant to absorb moisture prematurely. Another possibility is that the regeneration of the desiccant is incomplete or contaminated. If the dew point reading is close to the return air dew point reading, it indicates that the regeneration air circuit is completely ineffective or the desiccant is seriously polluted.
|
|
|
|