This form is widely used due to its strong adaptability. The drying box of the device is of a tray rack type, and the tray rack can be a fixed type or a mobile type installed on a trolley. The box freeze-drying process is roughly divided into three stages: pre-freezing, sublimation and heating;
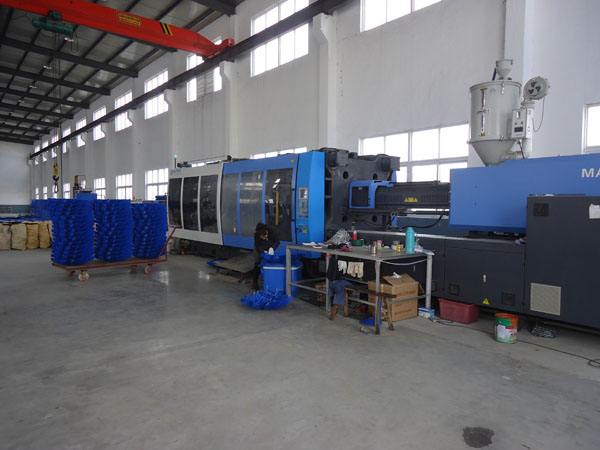 1. Pre-freeze first, and then vacuumize after freezing completely. Since the material contains a large amount of water, if it is first vacuumed, the gas dissolved in the water will quickly overflow due to the decrease of external pressure, forming bubbles and running away, and become boiling. At the same time, when the water evaporates into steam, it absorbs its own heat and forms ice. The ice re-vaporizes. The product produces many pores due to internal foaming and vaporization, which does not meet the process requirements. The pre-freezing temperature is about 5°C lower than the eutectic point of the material. Generally, the pre-freezing temperature is -30°C. If the temperature does not meet the requirements, the freezing will not be complete. The disadvantages are as mentioned above. The pre-freezing time is about 2h. Because the temperature of each shelf is different, sufficient time should be given, starting from the temperature below the eutectic point. The pre-freezing speed is controlled at 1~4°C per minute. Too high or low is not good for the product. Different product pre-freezing speeds are determined by experiments. This process is cooling and rising speed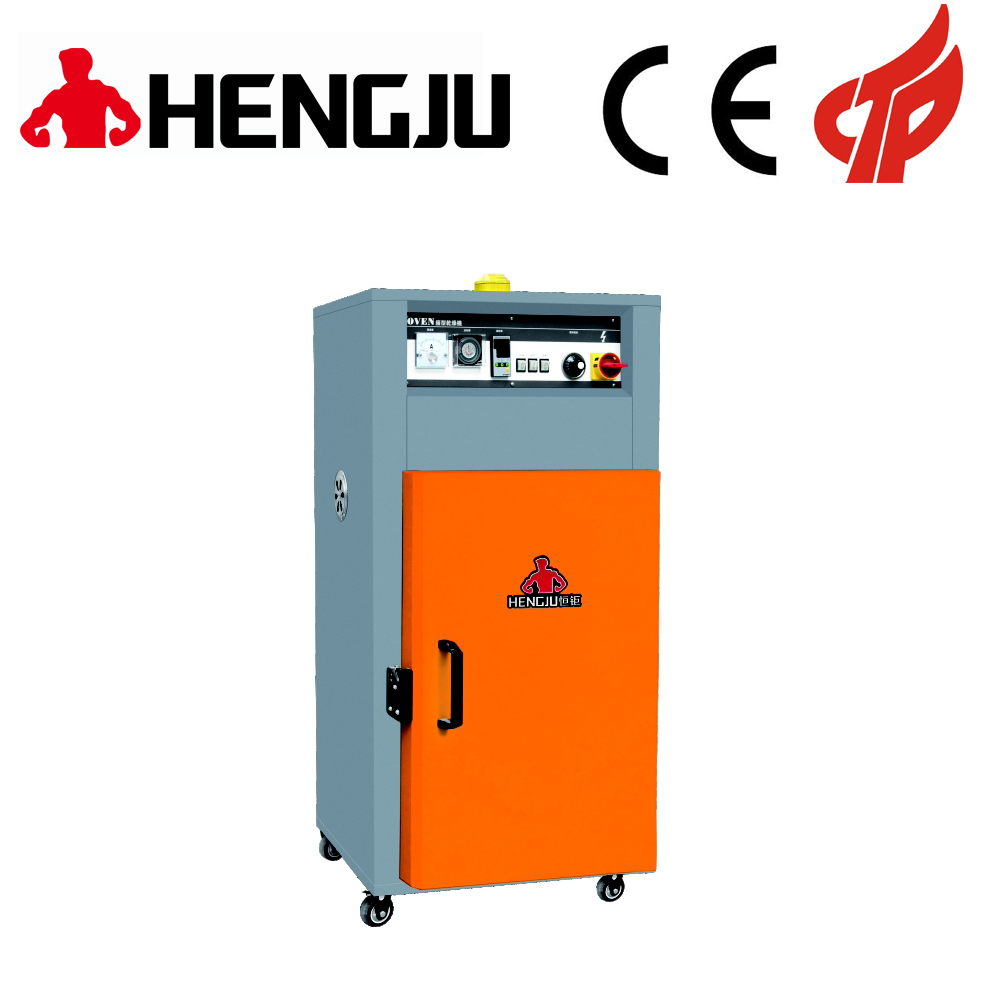 2. The sublimation process, after pre-freezing, is followed by vacuuming and entering the second stage, the temperature is almost unchanged, and the process of excluding frozen water is a constant speed process. The direct vaporization of ice also needs to absorb heat. At this time, heating is started to keep the temperature close to but below the eutectic temperature. If the heat is not given, the temperature of the material itself will drop, the drying speed will drop, and the time will be extended, and the product moisture will be unqualified. If heating is too much or too much, the temperature of the material itself will rise, exceed the eutectic point, melt locally, shrink in volume and foam. Because 1g of ice produces 9500L of water vapor at 13.3pa, the volume is large, and it is impossible to exclude it with ordinary mechanical pumps, and the use of steam jet pumps requires high-pressure steam to make ice frost, and keep it at -40℃ or lower. Steam in the condenser When the pressure drops at a certain level, the steam pressure in the drying box is high, forming a pressure difference, so a large amount of water vapor continuously enters the condenser. 3. The third stage is heating, and the remaining water evaporates. Since the frozen water has completely evaporated and the product has been shaped, the heating speed can be accelerated. When evaporating the unfrozen moisture, the drying speed will drop, the moisture will be continuously removed, and the temperature will gradually rise (generally not more than 40°C), and the temperature will stay at 30~35°C for 2~3h, and the drying will end. At this time, the vacuum can be broken, the finished product can be taken out, and the condenser can be heated under atmospheric pressure to melt the frost into water and remove it.
|