The determinants of a good drying efficiency have the following four points: drying temperature, drying time, air volume, and dew point. These four factors are interlinked, and any change in one condition will affect the drying effect. Drying temperature refers to the temperature of the air entering the drying barrel. Due to its physical properties, such as molecular structure, specific gravity, specific heat, moisture content and other factors, the drying temperature has certain restrictions. If the temperature is too high, the raw material Part of the additives volatile or agglomerated, too low will make some crystalline raw materials unable to reach the required drying conditions, such as: PC/120℃, ABS/80~95℃. In addition, insulation is required in the selection of dry barrels to avoid loss of drying temperature, resulting in insufficient drying temperature or waste of energy. Drying time: refers to the pre-drying time of raw materials before molding. Too long drying time will cause raw materials to deteriorate or agglomerate or waste energy. Too short drying time will cause excessive moisture content. For example: PC/3-4 hours, ABS/3-4 hours.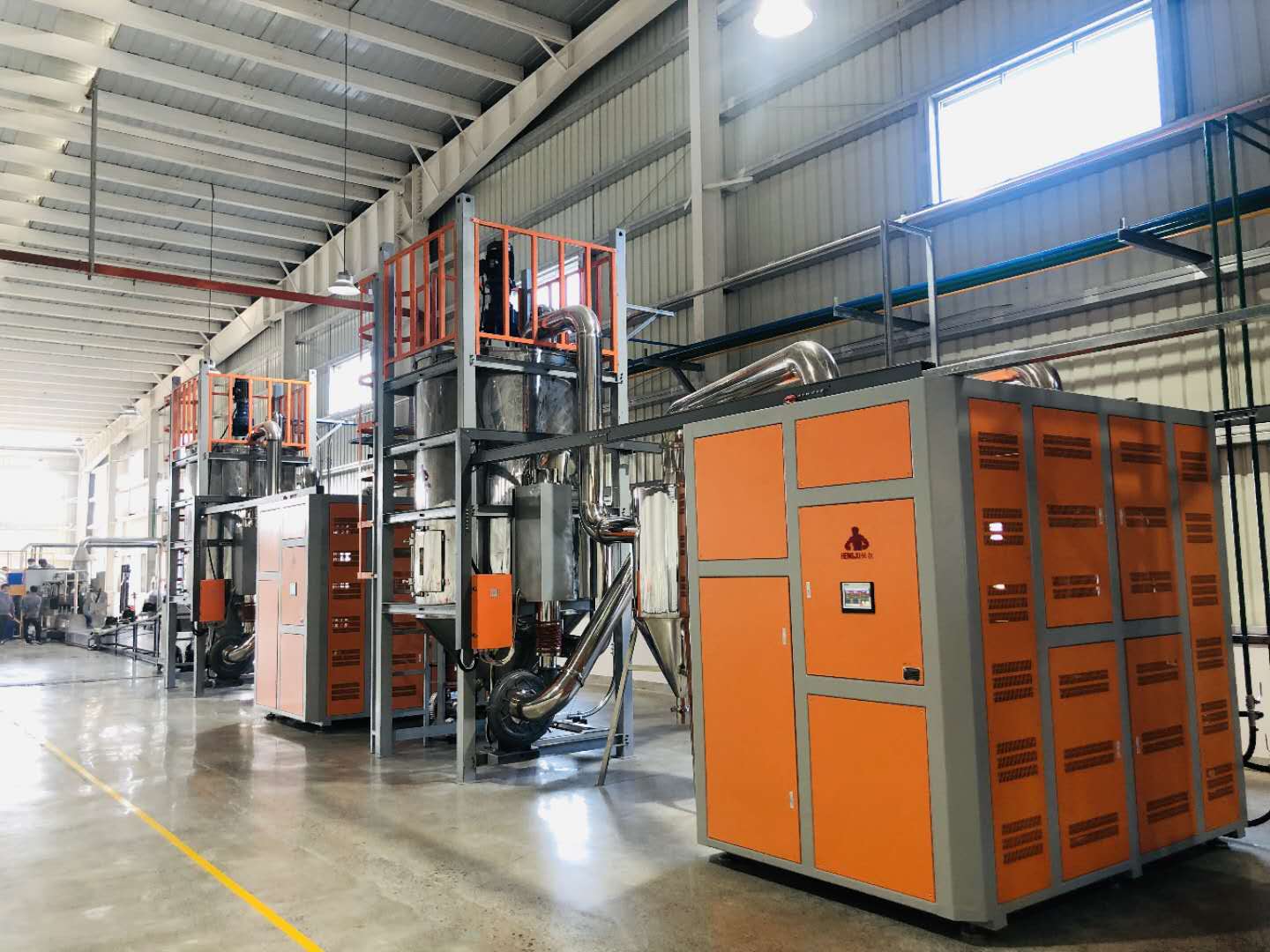 Air volume: It is the only medium that takes away the moisture in the raw materials. The air volume will affect the dehumidification effect. Too much air volume will cause the return air temperature to be too high, resulting in over heat and affecting the stability of the dew point. Too small air volume will not completely take away the moisture in the raw materials. The air volume also represents the dehumidification capacity of the dehumidifier dryer. Dew point temperature: refers to the temperature at which the moisture contained in the gas is condensed into water droplets when the gas is cooled. It is a unit for measuring the dryness (moistness) of the gas. The less moisture in the gas, the lower the dew point temperature. A good dehumidifier dryer must be able to reach a dew point temperature of -45°C.
|