Dehumidification and drying part: The hot and humid air coming back from the drying barrel is cooled and blown into the honeycomb runner. The moisture in the air is absorbed by the runner and then desorbed by the regenerated heated air. The two airflows act on the runner at the same time, and with the rotation of the runner, the moisture in the air is continuously adsorbed and desorbed by the regeneration air to be discharged, forming a stable low dew point air, which is heated to the plastic The drying temperature is blown into the drying barrel to form a closed cycle to dry the raw materials. Suction part: Suction material is sucked into the drying bucket from the storage bucket or other storage silo container. When the reed switch of the vacuum hopper detects that there is no material, the suction motor runs to generate a vacuum in the vacuum hopper. The raw materials in the storage bucket are sucked into the vacuum hopper due to the pressure difference of the air. When the suction time is completed, the suction motor stops running, and the raw materials fall into the drying bucket due to its own weight. The dried raw materials are drawn from the drying barrel to the electric eye hopper installed in the plastic molding machine.
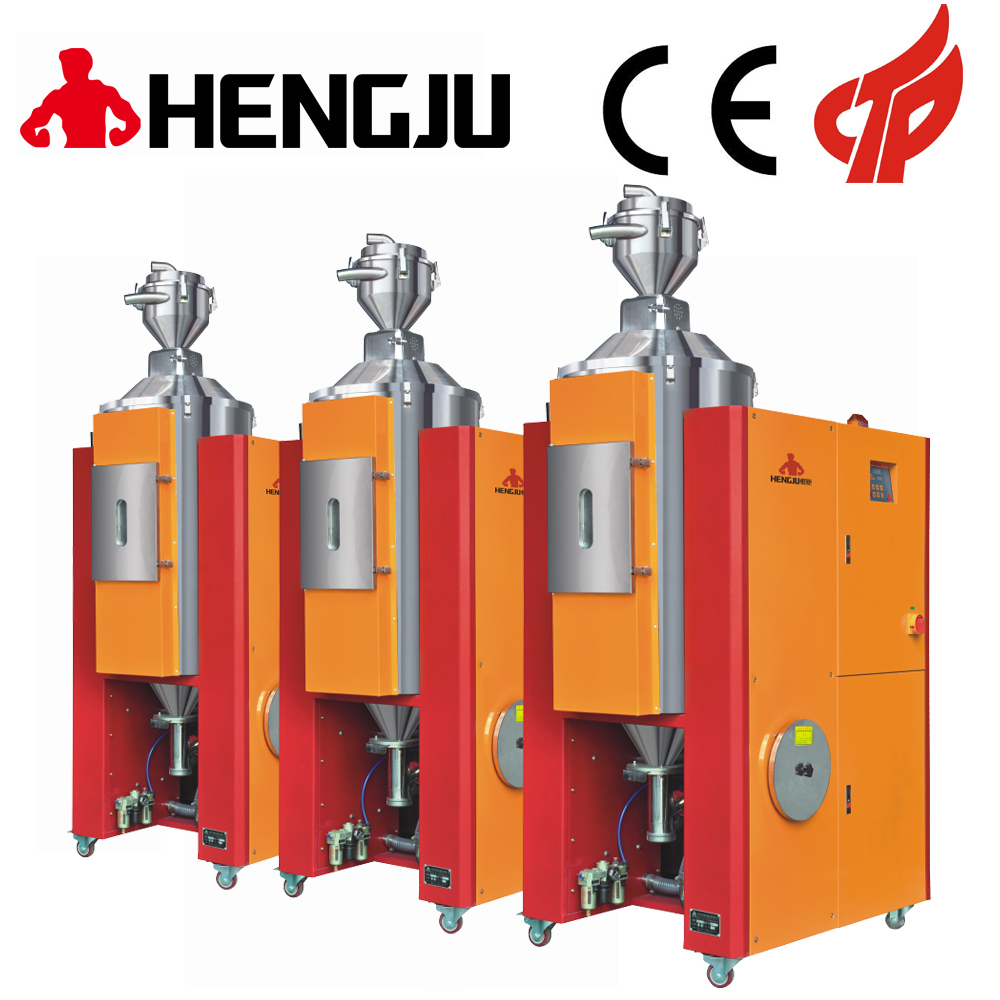 1. It integrates three functions of dehumidification, drying and two-stage feeding; 2. The dehumidification part is equipped with a wheel device, which can provide stable and low dew point air, and the dew point can reach below -50 ℃; 3. The stainless steel double-layer heat preservation drying barrel adopts the design of lower blowing pipe to make the raw materials evenly dry and effectively prevent heat loss; 4. The feeding system is equipped with a shutoff valve to ensure that there is no residual raw material in the material pipe; 5. The closed loop feeding system can prevent the raw materials from being polluted or damp; 6. The optical-grade model is equipped with a boiling electric eye hopper, which can remove the fine powder in the raw material, and can avoid the generation of stains in the molding of optical-grade products; 7. The optical-grade model system is equipped with high-precision and high-efficiency filters, which can effectively filter dust ions up to 0.3μm, and the filtration rate can reach 99.9%; 8. PLC control with LCD touch-sensitive man-machine interface can be purchased, the operation is centralized and convenient, and the whole machine can be controlled to run automatically; 9. Dew point detection device can be purchased; 10. Cyclone dust collector, oil filter and other accessories can be purchased; Relative humidity and dew: Relative humidity: The percentage of the actual water vapor density in the air and the saturated water vapor density at the same temperature is the relative humidity of the air. Dew point: refers to the temperature at which saturated water vapor condenses in the air. At a relative temperature of 100%, the ambient temperature is the dew point temperature. The lower the dew point temperature is than the ambient temperature, the lower the possibility of condensation, which means that the drier the air, the dew point is not affected by temperature, but affected by pressure. Precautions for fan use: 1. The fan will generate high temperature during use, please avoid touching the shell to avoid scalding; 2. The motor load current will vary with the air pressure used by the fan. When wiring, install an overload protection switch suitable for this model and use it at the rated full load current to avoid motor burnout; 3. In order to prevent hard objects, dust, powder particles, fibers and water droplets from being carried into the fan when the air enters the fan, thereby affecting the efficiency of the fan, the The machine is designed with an air filter, please clean the sundries in the air filter regularly (recommended once a week); 4. The internal and external surface dust of the fan should be cleaned regularly. If a large amount of dust accumulates, the poor heat dissipation effect will cause the temperature to rise, the air volume to decrease, and the vibration to increase. Cause mechanical failure; 5. If the operation is not smooth or abnormal noise occurs during use, please turn off the power for maintenance; Do not use the machine in the following situations: 1. There is a damaged line; 2. To prevent electric shock, do not run the machine on a wet floor or after the machine is exposed to rain; 3. If the machine is damaged or disassembled, it should not be overhauled and installed by professional maintenance personnel; 4. During the operation of the machine, at least 1m of surrounding space is required. Please protect this device and flammable materials at least 3m away; 5. Avoid vibration and magnetic influence in the work area;
|