The surface of ABS resin is easy to absorb moisture, causing defects such as scars and moiré on the surface of molded plastic parts. The drying temperature is 80-85°C for 2-4 hours. ABS is a water-absorbing plastic, at room temperature,
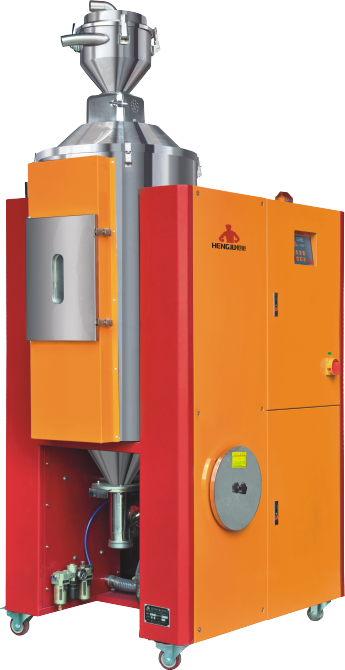 It can absorb 0.2%-0.35% moisture in 24 hours. Although this moisture does not have a significant impact on mechanical properties, if the humidity exceeds 0.2% during injection molding, the surface quality of the plastic will be greatly affected, so adequate drying should be carried out before processing Preheating and preheating can not only eliminate firework-like bubbles and silver wires on the surface of the part caused by water vapor, but also help plasticize the plastic and reduce the surface stain and moiré of the part. The moisture content of ABS raw materials should be controlled below 0.13%. The drying conditions before injection molding are: In the dry winter season, the temperature should be below 75~80 ℃, dry for 2~3h, In summer rainy days at 80~90 ℃, dry for 4~8h, If the part needs to achieve particularly excellent gloss or the part itself is complicated, the drying time is longer, up to 8-16h. Fogging on the surface of parts due to the presence of trace moisture is a problem that is often overlooked. It is best to convert the hopper of the machine into a hot air hopper dryer to prevent the dried ABS from absorbing moisture again in the hopper. However, this type of hopper should strengthen humidity monitoring to prevent overheating of the material when production is interrupted accidentally.
|