Manufacturing method of double crystal drying system for PET slice 【Technical Field】 [0001] The present invention relates to the field of PET chip drying, in particular to a dual crystal drying system for PET chips. 【Background technique】
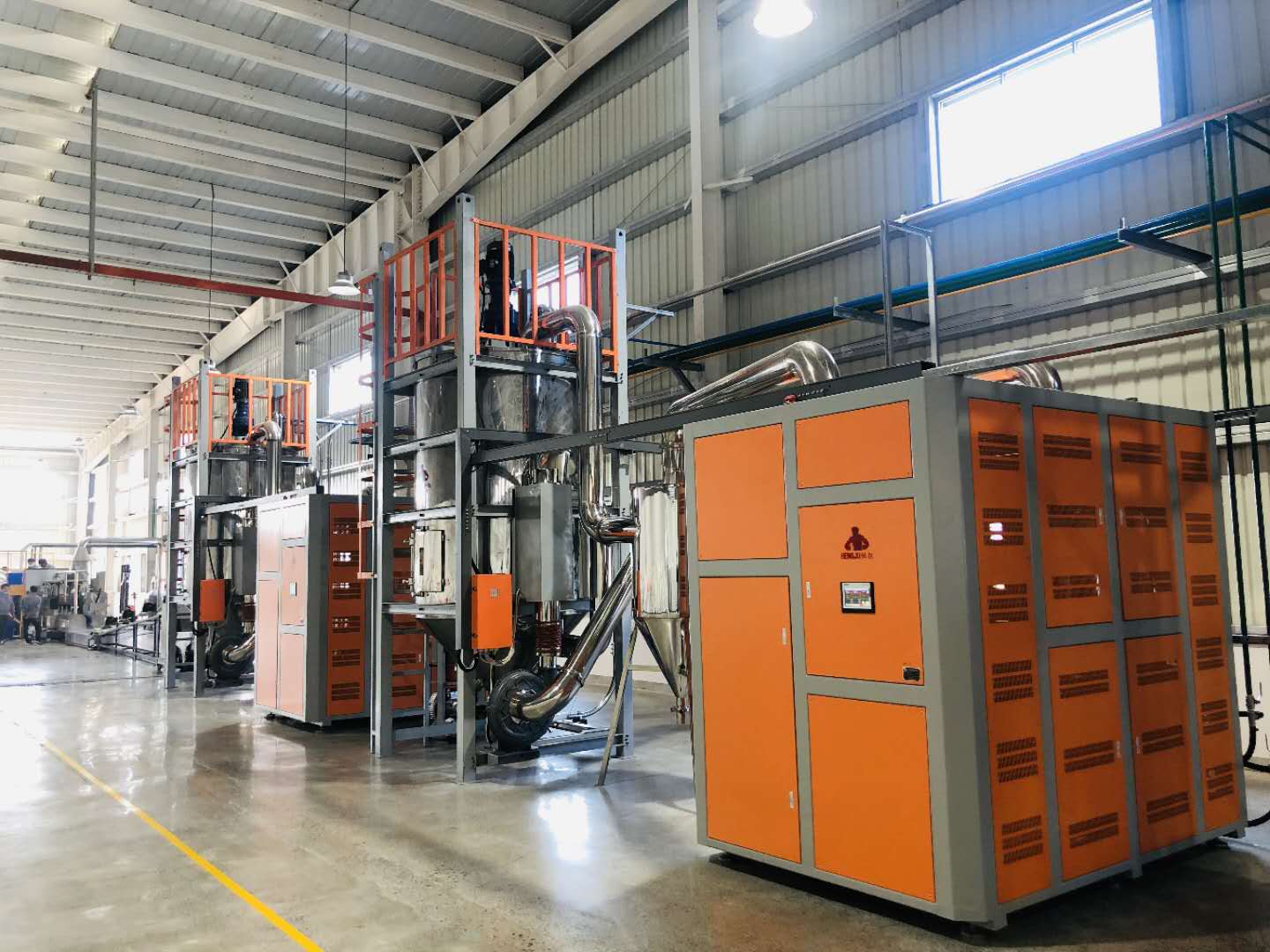 [0002] The crystallization and drying of polyester chips is an indispensable step in its processing and forming, because the moisture content of polyester is easily degraded into oligomers at high temperatures. In order to prevent the degradation of polyester during melt processing, it must be passed through Drying, at the same time, in order to prevent the polyester chips from agglomerating during the drying process, it must be crystallized before drying. BOPET production requires that the moisture content of the raw material resin be controlled below 50PPM before melt extrusion, so it needs to be crystallized and dried before production and processing. In the existing BOPET drying system, the low-amplitude crystallization bed has a long depth, and the amplitude of the raw material jump during the pre-crystallization process decreases with the depth of the crystallization bed, and it is easy to cause agglomeration when the raw material is not completely crystallized. In addition, the traditional BOPET drying system has one crystallization bed corresponding to one drying tower. A single set of crystallization system has great inconvenience to the development of product diversification and product production conversion, resulting in the limitation of product production types and the loss of waiting time for raw material drying during the conversion process. If multiple systems are configured to meet the needs of different products and increase output, each system requires a large amount of equipment, which requires a large amount of space and is equipped with sufficient personnel, resulting in more costs. [Utility model content] [0003] The purpose of the present utility model is to provide a dual crystal drying system for PET chips to solve the problems existing in the prior art. [0004] In order to achieve the above-mentioned purpose, the following technical solutions are adopted: including a first crystallization bed, a second crystallization bed and a drying tower, the outlet of the first crystallization bed and the outlet of the second crystallization bed are respectively connected to The inlet of the drying tower is connected. The first crystallization bed is a low-amplitude crystallization bed, the second crystallization bed is a high-amplitude crystallization bed, and the depth of the first crystallization bed is that of the second crystallization bed. 1.5-2.5 times, the amplitude of the second crystal bed is 1.5 to 2.5 times that of the first crystal bed. The specific size will be designed according to requirements and output. [0005] This utility model adopts a double crystallization bed structure. The crystallization beds with different amplitudes are suitable for different materials. When the two materials are converted into production, the crystallization beds can be used separately without cleaning the first material in the original crystallization bed. Then produce the second material. The first crystallization bed is mainly suitable for materials with high melting point and not easy to cause adhesion, such as ordinary PET bright raw materials. The second crystallization bed is mainly used for drying modified PET raw materials, such as heat-sealing raw materials. Partially modified resin pellets have higher TG, which tends to cause surface softening and bonding during the pre-crystallization process, resulting in agglomeration and clogging. The depth of the high-amplitude crystal bed is shorter, the amplitude is larger, and the crystal boiling efficiency is higher. , To prevent agglomeration during the crystallization process. [0006] Compared with the prior art, the present invention adopts two different crystallization beds, one of which has a shorter depth of crystallization bed, but a larger amplitude and higher crystallization boiling efficiency, which solves the problem of pre-crystallization and drying of raw materials. The problem of block; the double crystallization bed is equipped with the same drying tower, which can effectively and reasonably arrange the conversion of various types of products, use the time waiting for the drying of the raw materials in the production process, improve production efficiency, and save space, personnel and equipment costs. 【Detailed ways】 The utility model is further described. [, a dual crystallization drying system for PET chips, including a first crystallization bed 1, a second crystallization bed 2 and a drying tower 3. The outlet of the first crystallization bed I and the outlet of the second crystallization bed 2 are respectively connected to The inlet of the drying tower 3 is connected. The first crystallization bed is a low-amplitude crystallization bed, and the second crystallization bed is a high-amplitude crystallization bed. The depth of the first crystallization bed is 1.5 to 2.5 times that of the second crystallization bed. The amplitude of the bed is 1.5 to 2.5 times that of the first crystallization bed. The first crystallization bed is mainly suitable for materials with high melting point and not easy to cause adhesion. The second crystallization bed is mainly suitable for modified PET raw materials that are easy to bind and agglomerate, and the drying tower is shared. [0010] When the drying system is used, different crystallization beds are selected according to materials of different attributes. When the two materials are converted to production, there is no need to clean the first material in the original crystallization bed and then produce the second material. Use another crystallization bed directly. If the first crystallization bed processes ordinary PET raw materials and then prepares to process modified PET raw materials, close the discharge port of the first crystallization bed. There is no need to clean the first crystallization bed first, and directly put the modified PET raw materials in the second crystallization bed. After crystallization, open the outlet of the second crystallization bed and enter the shared drying tower from the inlet for drying. 【Sovereignty Item】 1. A dual crystallization drying system for PET chips, characterized in that it comprises a first crystallization bed, a second crystallization bed, and a drying tower. The outlet of the first crystallization bed and the outlet of the second crystallization bed are respectively Connected to the feed port of the drying tower, the first crystal bed is a low-amplitude crystal bed, and the second crystal bed is a high-amplitude crystal bed. The depth of the first crystal bed is 1.5-2.5 times that of the second crystal bed. The amplitude of the bed is 1.5-2.5 times that of the first crystallization bed. [Patent Abstract] This utility model relates to the field of PET chip drying, and specifically to a dual crystal drying system for PET chips, including a first crystallization bed, a second crystallization bed and a drying tower. The discharge port of the first crystallization bed, The discharge ports of the second crystal bed are respectively connected with the feed ports of the drying tower. The first crystal bed is a low-amplitude crystal bed, the second crystal bed is a high-amplitude crystal bed, and the depth of the first crystal bed is the second crystal bed. The amplitude of the second crystal bed is 1.5~2.5 times that of the first crystal bed. Compared with the prior art, this utility model adopts two different crystallization beds, one of which is shorter in depth, but larger in amplitude, and has higher crystal boiling efficiency, which solves the problem of agglomeration of raw materials during pre-crystallization and drying. ; The double crystallization bed is equipped with the same drying tower, which can effectively and reasonably arrange the conversion of various types of products, use the time waiting for the drying of the raw materials during the production process, improve production efficiency, and save space, personnel and equipment costs.
|