Circulating dehumidification drying system [Patent Abstract] A circulating dehumidification and drying system of the present invention includes a control system, a storage box, a drying cylinder, and a conveying mechanism for generating a negative pressure on the drying cylinder; the conveying mechanism is connected to the control system , The storage box is directly connected with the drying cylinder through a feed pipe. Compared with the prior art, the circulating dehumidification and drying system of the present invention eliminates the material cup above the drying cylinder, and directly feeds the material to the drying cylinder through the feed tube, the structure is simpler, and the production cost is reduced; The resin pellet raw material directly impacts the metal cup wall of the cup at high speed, reducing the maintenance cost of the cup; and the resin raw material directly impacts the original resin pellet raw material in the drying cylinder, which also prevents the resin pellet raw material from hitting the cup wall. The phenomenon of powdering improves the quality of resin pellet raw materials. 【Patent Description】 A circulating dehumidification drying system Technical field [0001] The present invention relates to the technical field of dehumidification and drying, in particular to a circulating dehumidification and drying system. 【Background technique】 [0002] Many granular materials must be dehumidified and dried before molding to ensure the transparency and smoothness of plastic products. The dryer is the main container for drying plastic materials in the plastic drying system. After the plastic materials enter the dryer, the plastic drying system blows hot air into the dryer to achieve the drying of the plastic materials. At present, dehumidification dryers in the plastic auxiliary machinery industry are basically equipped with a dedicated dehumidification source, a drying cylinder, a drive fan, an air circulation pipeline, and two small cups for automatic transportation (the first cup installed above the drying cylinder , The second material cup installed above the host, the output port of the first material cup is connected to the drying cylinder, the input port of the second material cup is connected to the drying cylinder, and the output port of the second material cup is connected to the host), resin particles The raw materials arrive at the first bowl first. After the first bowl is loaded with the preset volume of raw materials, the output port of the first bowl is opened, and the raw materials enter the drying cylinder for drying; then the dried raw materials in the drying cylinder are transferred to the second The material cup is used by the host. That is to say, in the current field of dehumidification and drying of rubber particles, there is a conveying cup for conveying resin particles on the top of the drying cylinder. However, when the material cup is used to transport the resin particle material, the resin particle material will directly impact the side wall of the metal material of the material cup at high speed, and the side wall of the material cup will be obviously worn through after several years of use, shortening The service life of the material cup increases the maintenance cost of the equipment; and the impact of the raw material on the wall of the material cup will cause the powder of the resin particle raw material and affect the quality of the resin particle material. [Content of the invention]
[0003] In view of the above-mentioned technical problems in the prior art, the present invention provides a circulating dehumidification and drying system that can automatically transport raw materials, reduce equipment maintenance costs, and ensure the dehumidification and drying quality of granular raw materials. [0004] In order to achieve the above object, the present invention provides the following technical solutions: Provide a circulating dehumidification drying system, including a control system, a storage box, a drying cylinder, and a conveying mechanism for generating a negative pressure on the drying cylinder; The conveying mechanism is connected with the control system, and the storage box is directly connected with the drying cylinder through a feed pipe. [0005] Wherein, one end of the feed pipe is in communication with the bottom outlet of the storage tank, and the other end of the feed pipe is in communication with the top inlet of the drying cylinder. [0006] Wherein, it also includes a dehumidification and drying mechanism connected to the control system and capable of dehumidifying and heating the inlet air of the drying cylinder, the dehumidification and drying mechanism including an air inlet pipe, a drying fan, an air outlet pipe, and a heating pipe One end of the air inlet pipe is connected to the drying fan, the other end is connected to the upper part of the inner cavity of the drying cylinder, one end of the air outlet pipe is connected to the drying fan, and the other end is connected to one end of the heating tube, The other end of the heating tube is connected to the lower part of the inner cavity of the drying cylinder. [0007] Wherein, a first filter is provided between the intake pipe and the drying fan, and a second filter is provided between the heating pipe and the drying cylinder. [0008] Wherein, the dehumidification and drying mechanism further includes an inert gas machine for generating inert gas, the inert gas machine is in communication with the gas outlet pipe, and a cutoff is sequentially connected between the inert gas machine and the gas outlet pipe. Valves and flow valves.
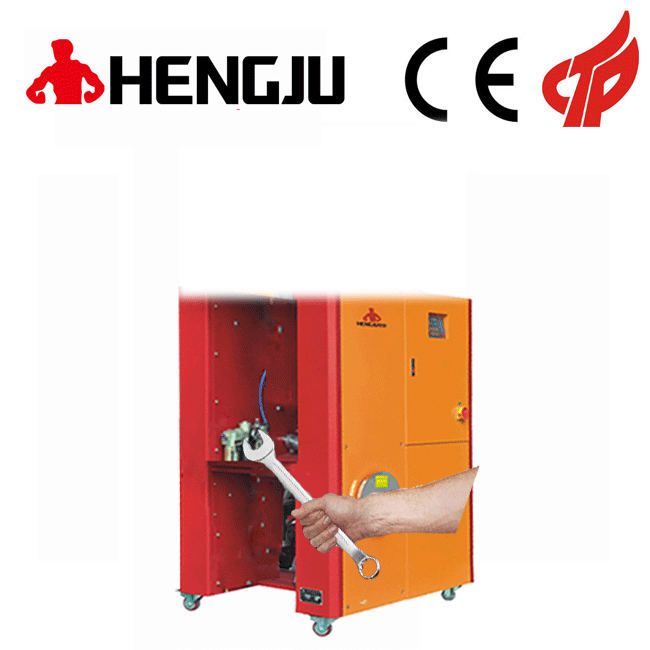 [0009] Wherein, the entire circulating dehumidification and drying system is airtightly arranged, and the inert gas is located anywhere in the system. [0010] Wherein, the circulating dehumidification drying system further includes a host, a material cup is arranged above the host, the bottom outlet of the drying cylinder is connected to the material cup through a pipe, and the conveying mechanism is connected to the material cup connection. [0011] Wherein, the conveying mechanism includes a conveying fan, a first air path and a second air path, and the first air path is sequentially connected to the drying cylinder, the first direction reversing valve, the conveying fan, and the second air path. The direction reversing valve and the storage box, and the second air path connects the material cup, the first direction reversing valve, the conveying fan, the second direction reversing valve and the outside in sequence. [0012] Wherein, the first direction reversing valve of the first gas path is connected to the drying cylinder through a third filter. [0013] Wherein, the circulating dehumidification and drying system further includes a frame, and the conveying mechanism, the dehumidification and drying mechanism, and the control system are all connected to the frame. [0014] The beneficial effects of the present invention: The present invention provides a circulating dehumidification drying system. During operation, when the drying cylinder needs to be fed, the control system controls the conveying mechanism to pump the inner cavity of the drying cylinder to a negative pressure. Under the action of pressure, the granular material in the storage box enters the drying cylinder through the feed pipe. When the drying cylinder is full of materials, the control system controls the conveying mechanism to stop feeding to the drying cylinder; when the granular material needs to be dehumidified and dried, the dehumidifying and drying mechanism will enter the drying cylinder. The wind of the drying cylinder is dehumidified and heated, and the hot air after the dehumidification and heating treatment enters the drying cylinder and dehumidifies and dries the material. The moisture is then extracted by the dehumidification and drying mechanism to form a dehumidification and drying circulating gas flow. Compared with the prior art, the circulating dehumidification drying system of the present invention eliminates the material cup above the drying cylinder, and directly feeds the material to the drying cylinder through the feed pipe. The structure is simpler and the production cost is reduced; The pellet raw material directly impacts the metal cup wall of the feed cup at high speed, thereby reducing the maintenance cost of the feed cup; and it also avoids the pellet raw material directly impacting the original pellet raw material in the drying cylinder, and also prevents the resin pellet raw material from hitting the cup The phenomenon of pulverization of the wall improves the quality of the resin particles. 【Explanation of drawings】 [0015] FIG. 1 is a schematic structural diagram of a circulating dehumidification and drying system of the present invention. [0016] Reference signs: control system 1; sensor 2; storage box 3; drying cylinder 4; conveying mechanism 5, conveying fan 51, first direction reversing valve 52, second direction reversing valve 53, third filter Air volume control valve 55, metering valve 56; dehumidification and drying mechanism 6, air inlet pipe 61, drying fan 62, air outlet pipe 63, heating pipe 64, first filter 65, second filter 66; inert gas machine 7, Stop valve 71, flow valve 72; host 8, material cup 81; piping 9, feed pipe 91, elbow 911; frame 10. 【detailed description】 [0017] The present invention will be described in detail below in conjunction with specific embodiments and drawings. [0018] A cyclic dehumidification and drying system of this embodiment, as shown in FIG. 1, includes a control system 1, a sensor 2, and a storage box 3. Drying cylinder 4, conveying mechanism 5 for generating negative pressure of drying cylinder 4, and dehumidifying and drying mechanism 6 capable of dehumidifying and heating the inlet air of drying cylinder 4; sensor 2, conveying mechanism 5 and dehumidifying and drying mechanism 6 Both are connected to the control system I, and the storage box 3 is directly connected to the drying cylinder 4 through the feed pipe 91. One end of the feed pipe 91 is connected to the bottom outlet of the storage box 3, and the other end of the feed pipe 91 is bent and connected to the top center inlet of the drying cylinder 4. The bent pipe 911 makes the resin pellet raw material downward from the top of the drying cylinder 4. Conveying materials. The circulating dehumidification and drying system also includes a host 8 for using dehumidified and dried granular raw materials. A material cup 81 is arranged above the host 8. The bottom outlet of the drying cylinder 4 and the material cup 81 are connected through a pipe 9, and the conveying mechanism 5 is connected to The feed cup 81 is connected (because the main machine is a device that uses dehumidified and dried granular materials, without a barrel, the granular materials cannot hit the main machine, so there must be a cup to transport the raw materials). During work, when the drying cylinder 4 needs to be fed, the control system I controls the conveying mechanism 5 to pump the inner cavity of the drying cylinder 4 to a negative pressure. Under the negative pressure of the drying cylinder 4, the resin pellet material in the storage box 3 passes through The feed pipe 91 enters the drying cylinder 4. When the sensor 2 detects that the drying cylinder 4 is full of materials, the conveying mechanism 5 stops feeding the drying cylinder 4; when dehumidification and drying are required, the dehumidification drying mechanism 6 dehumidifies the wind entering the drying cylinder 4 And heating, the hot air that has been dehumidified and heated enters the drying cylinder 4 to dehumidify and dry the material, and the moisture is then extracted by the dehumidification and drying mechanism 6 to form a dehumidification and drying circulating gas flow. Compared with the prior art, the circulating dehumidification drying system of the present invention eliminates the material cup 81 above the drying cylinder 4, and directly feeds the material to the drying cylinder 4 through the feed pipe 91, which has a simpler structure and reduces production costs. It also avoids that the resin particle material directly impacts the side wall of the metal material cup at high speed, reducing the maintenance cost of the material cup; and, the resin material directly impacts the original resin particle material in the drying cylinder 4, which also prevents the resin particle material from impacting The phenomenon of pulverization of the material cup wall (the effect of particle material impacting the particle material, and the particle material impacting the stainless steel material cup wall is of course different), thereby improving the quality of the resin particle material. It should be supplemented that due to the inherent structure of the material cup, the granular raw materials in the prior art enter the material cup from the top of the material cup and then hit the side wall of the material cup; and the volume of the material cup is generally relatively small. All the raw materials in the material cup are discharged into the drying cylinder each time, so it is impossible to use the material cup to achieve the effect of the granular raw material directly hitting the original granular raw material in the present invention to prevent the particles from being pulverized. [0019] In this embodiment, the dehumidifying and drying mechanism 6 includes an air inlet pipe 61, a drying fan 62, an air outlet pipe 63, and a heating pipe 64. One end of the air inlet pipe 61 is connected with the drying fan 62 and the other end is connected to the inner cavity of the drying cylinder 4. The air outlet pipe 63 is connected to the drying fan 62 at one end, and the other end is connected to one end of the heating pipe 64, and the other end of the heating pipe 64 is connected to the lower part of the inner cavity of the drying cylinder 4. A first filter 65 is provided between the air inlet pipe 61 and the drying fan 62, and a second filter 66 is provided between the heating pipe 64 and the drying cylinder 4. The dehumidification and drying mechanism 6 also includes an inert gas generator 7 for generating inert gas. The inert gas is preferably nitrogen. The inert gas generator 7 is connected to the gas outlet pipe 63. The inert gas passes through the stop valve 71 and the flow valve 72 in sequence. The dehumidification and drying mechanism 6 forms a drying cycle system for dehumidification and drying. The circulating gas flow includes: drying cylinder 4—intake pipe 61—(first filter 65) 4 intake pipe 61—drying fan 62—outlet pipe 63—inert gas machine 7—heating pipe 64—(second filter 66) 4 drying cylinder 4. There are also conveying pipes 9 (collectively referred to as pipes used to transport raw materials) and fasteners connecting the dehumidifying and drying mechanism 6. The entire circulating gas flow is a complete closed structure, and the external or built-in nitrogen or dehumidified air is cut off The valve 71 and the flow valve 72 enter the drying cycle system. [0020] In this embodiment, the conveying mechanism 5 includes a conveying fan 51, a first air path and a second air path. The first air path is sequentially connected to the drying cylinder 4, the first direction reversing valve 52, the conveying fan 51, and the second air path. The direction reversing valve 53 and the storage box 3, and the second air path connects the material cup 81, the first direction reversing valve 52, the conveying fan 51, the first direction reversing valve 52 and the outside in sequence. The first direction reversing valve 52 of the first air path is connected to the drying cylinder 4 through a third filter 54. The conveying process of the conveying mechanism 5 mainly includes: storage box-drying cylinder 4 inlet-third filter 54-first direction reversing valve 52-conveying fan 51-second direction reversing valve 53-air volume regulating valve 55 Or dosing valve 56—transporting pipe 9—inlet pipe of drying cylinder 4 or material cup 81 above host 8. [0021] In this embodiment, the circulating dehumidification and drying system is airtight as a whole, and there is nitrogen at any place in the system. The traditional plastic desiccant dryer is not strictly a closed device. If nitrogen is directly flushed into the drying cycle pipeline, the original drying cycle will be destroyed, and the flushed nitrogen will be quickly discharged into the atmosphere. This is a waste of nitrogen resources, that is, a loss of cost. When developing the nitrogen dryer in this embodiment, the tightness of the entire structure is the key consideration. Any part of the entire dehumidification and drying system (including equipment and pipelines) must withstand a pressure of at least 5-10kpa, and the airtightness is better , The less nitrogen consumption in the dehumidifying and drying mechanism 6 is, the higher the nitrogen concentration. [0022] Nitrogen is a good inert gas. When making resin light guide plates, resin lenses, and high-specification transparent resin products, drying with nitrogen or flushing nitrogen into the screw of the injection molding machine can effectively prevent expensive resins from overheating or obsolescence. The resulting yellowing phenomenon greatly improves the product qualification rate and can greatly reduce the cost; and nitrogen can also reduce the yellowing of the metal screw of the injection molding machine and reduce the maintenance cost of the equipment. Among them, the nitrogen source in the nitrogen dryer is basically derived from the separation of compressed air. In terms of structure, there are liquid nitrogen storage tanks, membrane separation nitrogen (with a relatively compact structure), and double-tower molecular sieve nitrogen production. The nitrogen generated by the structure needs to be decompressed before being reused. [0023] In this embodiment, the circulating dehumidification and drying system also includes a frame 10 with casters. The conveying mechanism 5, the dehumidification and drying mechanism 6 and the control system 1 are all connected to the frame 10, and the entire structure is more compact and flexible. [0024] Finally, it should be noted that the above embodiments are only used to illustrate the technical solutions of the present invention, rather than to limit the scope of protection of the present invention. Although the present invention has been described in detail with reference to the preferred embodiments, common techniques in the field Personnel should understand that the technical solution of the present invention can be modified or equivalently replaced without departing from the essence and scope of the technical solution of the present invention. 【Sovereignty Item】 1. A circulating dehumidification and drying system, characterized in that it includes a control system, a storage box, a drying cylinder, and a conveying mechanism for generating negative pressure in the drying cylinder; the conveying mechanism is connected to the control system, The storage box is directly connected with the drying cylinder through a feed pipe. 2. A circulating dehumidification drying system according to claim 1, characterized in that: one end of the feed pipe is in communication with the bottom outlet of the storage tank, and the other end of the feed pipe is connected to the drying The top inlet of the barrel is connected. 3. A circulating dehumidification and drying system according to claim 1, characterized in that: it further comprises a dehumidification and drying mechanism connected to the control system and capable of dehumidifying and heating the inlet air of the drying cylinder, the The dehumidification and drying mechanism includes an air inlet pipe, a drying fan, an air outlet pipe, and a heating pipe. One end of the air inlet pipe is connected to the drying fan, and the other end is connected to the upper part of the inner cavity of the drying cylinder. The drying fan is connected, the other end is connected to one end of the heating tube, and the other end of the heating tube is connected to the lower part of the inner cavity of the drying cylinder.
|