Most engineering plastics and plastic alloy pellets contain different degrees of moisture, and the moisture is distributed on the surface of the plastic pellets and inside the plastic pellets. If the plastic pellets are not dried well, the internal quality and appearance quality of the plastic products are both Have an impact and cause processing difficulties. The internal quality of plastic products shows that its various performance indicators are significantly reduced, the internal stress increases, and it is easy to crack, which promotes the hydrolysis and degradation of the polymer; the appearance quality shows that the product is yellow, producing bubbles, blemishes, silver threads, markings, and Transparency has declined. Due to the presence of moisture, the apparent viscosity of the plastic melt fluctuates irregularly during the injection molding and extrusion molding process, and the melt sticks to the runner, sometimes serious salivation, which makes it difficult to mold. For most engineering plastics and plastic alloys, strict drying is particularly important! Especially for recycled plastics, after cleaning, granulation and other regeneration processes, the moisture content greatly exceeds the standard, and strict drying is required.
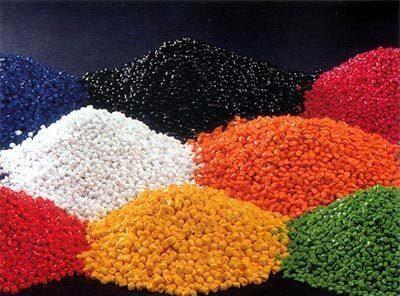 The maximum allowable moisture content of common plastics: 01 What is the specificity of plastic pellet drying? The initial moisture content in the plastic pellets is relatively low, only 0.5% to 1.0%, so the drying of plastic pellets is a trace moisture drying. The drying method used is mostly thermal dehumidification, and the drying medium is mostly hot air. The drying temperature is average. 80~150℃. Due to the low initial moisture content of the pellets, in the closed-circuit drying cycle system, after the moisture evaporates and vaporizes into the hot air, the hot air is still far from the saturated state (quantitative calculation is omitted), and it still has a strong mass transfer driving force. . In order to obtain high-performance and high-quality plastic products, the maximum allowable moisture content of engineering plastics is very low (0.02%~0.08%), which results in a long time for the slow-down drying stage. This is due to the slow diffusion of moisture from the inside of the particle to the surface to vaporize, the surface of the wet particle gradually changes, and the vaporized surface moves to the inner layer.As the moisture content inside the particle decreases, the rate of its transfer to the surface gradually decreases, so the drying rate It is getting lower and lower, and the drying time becomes longer and longer. 02 What kind of drying methods and equipment can meet the drying of plastics? In order to accelerate the heat transfer of the plastic pellets, increase the vaporization of the water inside the plastic particles to the surface and quickly take away the water vapor, the following 4 methods and equipment are generally used. The plastic pellets of the rotary vacuum dryer are put into the drum, while heating and vacuuming. Relying on heat conduction to transfer heat, drying relies on vacuum to increase △p (the difference between the partial pressure of water vapor on the surface of the plastic particles and the partial pressure of water vapor in vacuum). The efficiency and speed of this type of equipment are not as good as the following three types, and the equipment investment is large. Dehumidifying air dryer
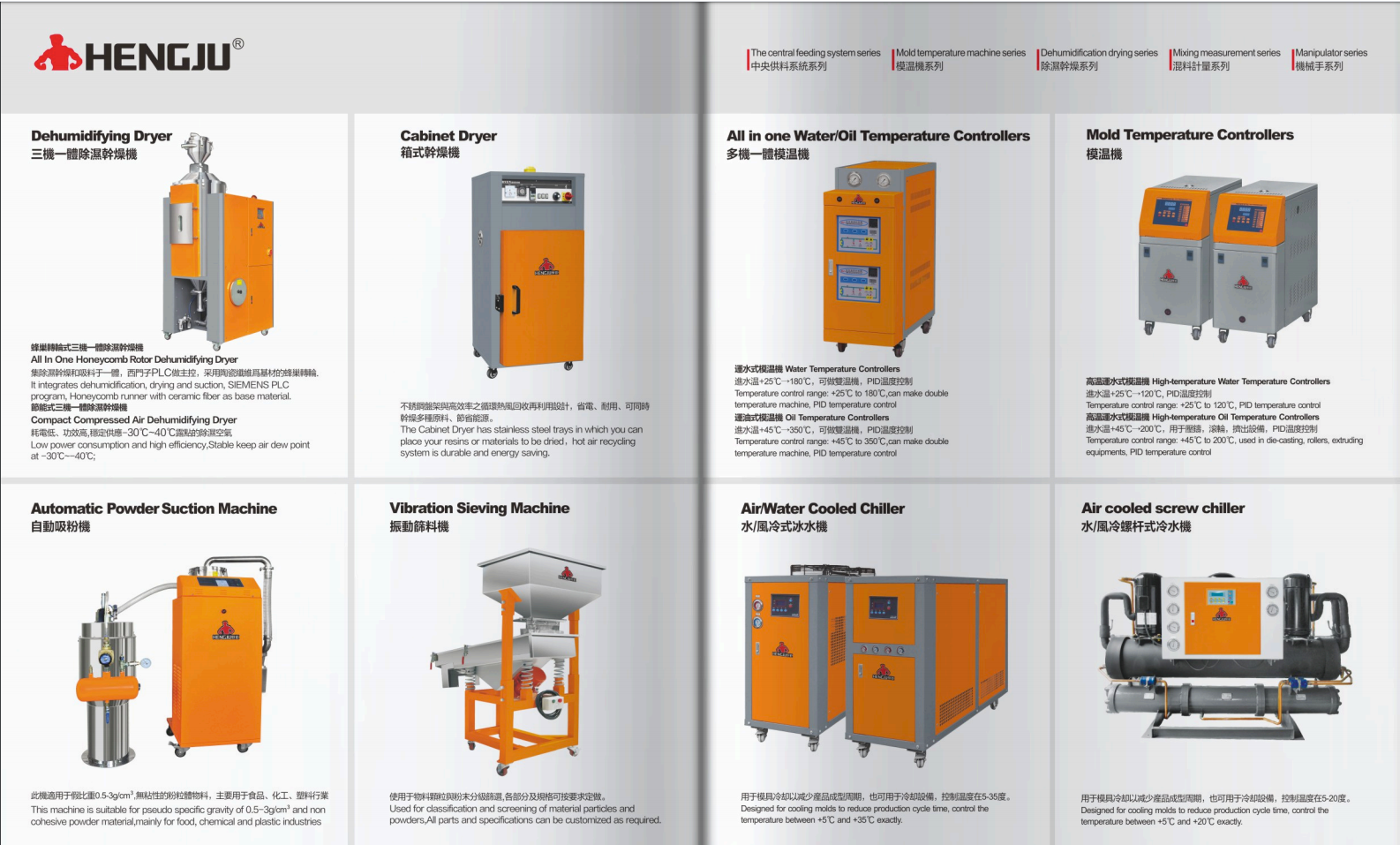 The plastic particles are statically accumulated in the barrel, and the heated air dehumidified and heated by the molecular sieve flows through the plastic particle layer from bottom to top, and the molecular sieve after moisture absorption can be reused by heating and regeneration. The heat transfer of this kind of equipment relies on convection heat transfer, and the drying relies on molecular sieve dehumidification to increase △p. This kind of equipment is mostly used internationally, and most domestic manufacturing plants with high drying requirements also use this kind of equipment. The high-speed hot air flow of the boiling dryer is blown from bottom to top through the porous plate, and the plastic granules are fluidized on the upper part of the porous plate. The heat transfer relies on high-speed convection heat exchange, and the drying relies on the high-speed air flow through the entire surface of the plastic granules, and energy saving depends on Circulating use of closed-circuit hot air. Dielectric and microwave heating and drying place the polar plastic pellets in a high-frequency alternating electric field. Affected by the electric field, the plastic molecules will rearrange, and internal friction will generate heat. Its characteristic is that the heat is generated in the quality of all materials, and the highest temperature appears in the center of the plastic pellet, which is exactly the opposite of the above three heat transfer processes. There are few reports on the industrialization of this method in the world.
|